Proven methods
for removing chloride and potassium from the recovery loop.
In modern kraft recovery operations, the key sodium and sulfur compounds from the fiberline are recovered and regenerated to minimize the need for makeup chemicals – and to also produce renewable energy in the process. Chemical recovery loops are becoming more and more efficient such that emissions, effluents, and waste streams are minimized.
THE LABYRINTH BREAKTHROUGH
In collaboration with research institutes, ANDRITZ tested different variations of diffuser block and nozzle geometries. In 2013, there was a breakthrough. A new type of diffuser block was produced with a labyrinth geometry.
Numerous tests were conducted on a prototype unit to confirm the CFD simulations. Figure 1 shows the prototype with eight diffusers in the block and a labyrinth with three expansion chambers. Extensive tests confirmed that the labyrinth renders the flow absolutely evenly.
A range of very thin to very thick coating layers can now be applied with high profile accuracy to eliminate defects or streaks. The deviations in CD profile are typically in the range of ± 1% for coating weights between 2 gsm to 14 gsm.
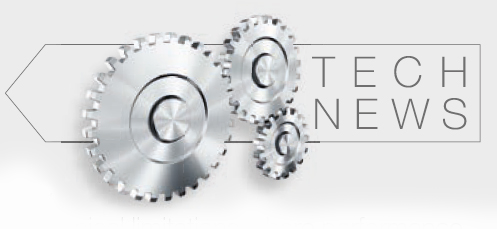
REMOVE AND RECOVER
ANDRITZ offers two economic and environmentally attractive solutions to effectively remove chlorides and potassium and recover sodium and sulfate from the ESP ash. Selecting the most suitable technology for a mill is always case-specific, depending mainly on removal capacity needs and mill process characteristics.
The recovery of process elements and the removal of non-process elements are possible primarily due to the solubility differences between alkali sulfates and alkali chlorides. The general idea is that chloride and potassium are removed as liquids, while most of the valuable sodium and sulfate is recovered as solids and led back to the chemical recovery cycle.
Figure 1: Simplified flowsheet of the ALE process.
ASH LEACHING (ALE) TECHNOLOGY
For lower capacity requirements and generally for retrofit installations, the ALE process is less expensive to install and assembly is simpler. In ash leaching, the ESP ash is partially dissolved in hot secondary condensate from the evaporators. After partially dissolving, the solids and liquid are separated using a centrifuge. The solids consist mainly of sodium sulfate while the filtrate is rich in chloride and potassium.
After separation, the solids are mixed with heavy black liquor. A part of the liquid fraction is purged from the system to remove Cl and K. The rest of the filtrate is recycled to the leaching tank in order to prevent excess dissolution of sodium from the ESP ash.
A typical ALE system has removal efficiency of 85% with a sodium loss of 25%. The best performance can be reached by optimization of the ash water ratio and recirculation to the leaching tank.
ASH RECRYSTALLIZATION (ARC) TECHNOLOGY
A typical ARC system has removal efficiency of 90% with a sodium loss of 20%. ARC technology can also handle larger capacities, making it the better choice for larger retrofits or greenfield installations.
In the ARC process, the ash is completely dissolved in clean condensate (or another calcium-free water source). After dissolving, the ash solution is pumped to a crystallizer where water is evaporated until sodium sulfate precipitates from the solution. Precipitated crystals are sent to a thickener and separated with a pusher centrifuge. Most of the separated liquid is recirculated to the crystallizer to minimize sodium losses. The remaining liquid is purged to remove dissolved chloride and potassium from the liquor cycle.
Figure 2: Simplified flowsheet of the ARC process.
CONCLUSION
The ALE process is relatively simple, and well proven. Its small footprint is ideal for retrofits and is more readily integrated into an existing recovery boiler layout. When the need for ash treatment capacity increases, the solid-liquid separation of the leaching system can become a bottleneck.
The ARC process is generally more suitable for larger chloride and potassium removal needs. Evaporated crystals are also predominantly pure sodium sulfate (Figure 5), so the recovery and removal efficiencies are also better.