Life Cycle Service
We understand service as an inseparable link in the long-term partnership with you – our esteemed customer.
ANDRITZ Life Cycle Service is a dedicated partner to support your production success during the life cycle of our products.

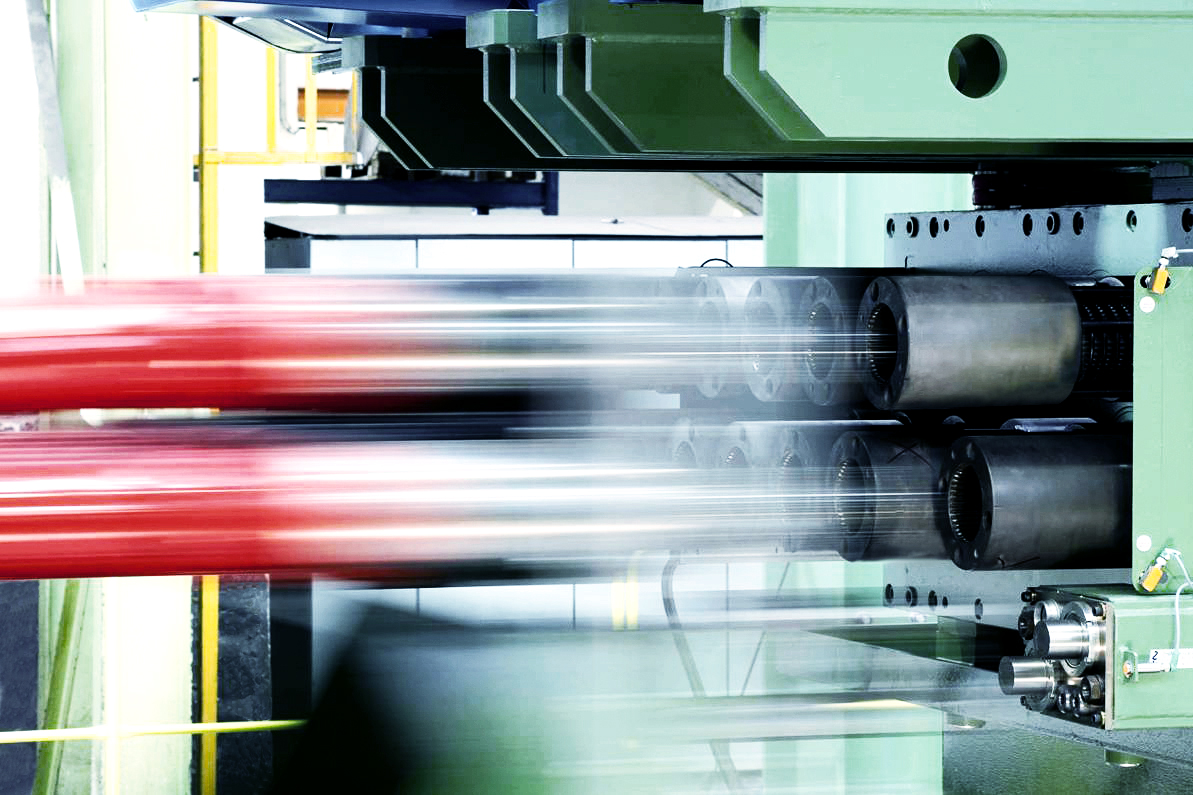
Each customer is unique, and so is our life cycle service support and assistance. We provide expertise for all spare parts, maintenance, retrofit, and upgrade needs. Our wide and longstanding knowledge and proven concepts combined with ANDRITZ technology provide the basis of our support to meet customers’ production targets as well as achieving maximum mill utilization and efficiency.
Operational services
- OEM parts
- Spare and wear parts
- Engineered/know-how parts
Plant and equipment upgrades
- Equipment and system upgrades (e.g. upgrading original ARP through new process to reduce HCL and dust exhausting to apply newest national standard)
- Rebuilds, revamps, and retrofits (e.g. on original rolling mill, new shape meter control system added to higher production capacity and increase strip quality)
- Automation and process upgrades, as well as improvements (e.g. ECOmode for HCl Regeneration Plants, Advanced Furnace Control)
- SV services and quality control
Maintenance and operation services
- Field services, optimization, training
- Process performance and improvement studies
- Maintenance contracts and studies
Condition and process monitoring
- Online diagnostics and process monitoring – Acoustic Emission (AE) based
- Improvement of processes and product quality
- Prevention of unplanned downtimes
- Improvement of spare-part stock holding