It's Super Duplex
Duplex stainless steels are a family of grades combining good corrosion resistance with high strength and ease of fabrication. The term “duplex” (lat. for “double”) refers to the steel grades that have a two-phase microstructure consisting of ferrite and austenite.
The aim is usually to produce a 50/50 mix, although in commercial alloys the ratio may be 40/60. Duplex stainless steels have roughly twice the strength compared to austenitic stainless steels and also improved resistance to localized corrosion, particularly pitting, crevice corrosion and stress corrosion cracking. They are characterized by high chromium (19–32%) and molybdenum (up to 5%) and lower nickel contents than austenitic stainless steels. The properties of duplex stainless steels are achieved with overall lower alloy content than similar performing super-austenitic grades, making their use cost-effective for many applications. Duplex grades are differentiated based on their alloy content and corrosion resistance. The different grades, which range in corrosion performance, depending on the composition of its alloys, are Lean Duplex, 2205 Grade, Super Duplex and Hyper Duplex. Their physical properties are between those of the austenitic and ferritic stainless steels, but tend to be closer to those of the ferritics and to carbon steel. The most important alloying elements in the duplex production are chromium, molybdenum, nitrogen and nickel. The amounts of these elements within the alloying determine the grade of duplex stainless steel.
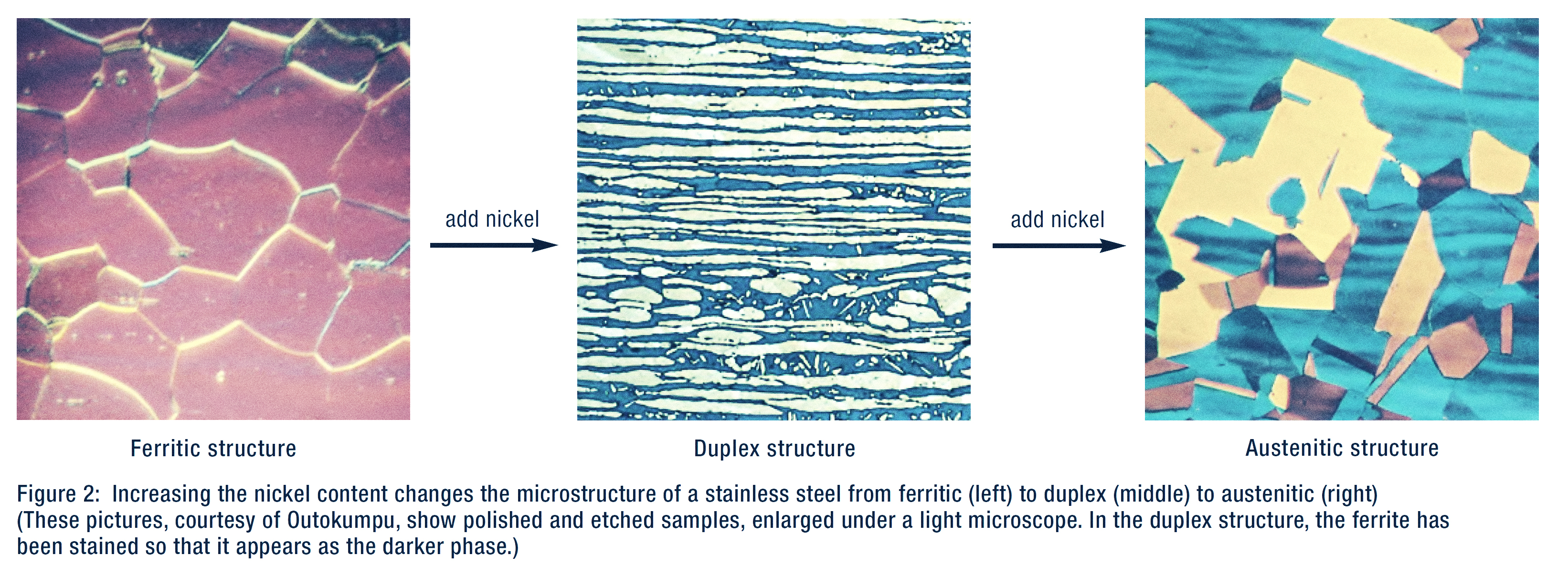
Increasing the nickel content changes the microstructure of a stainless steel from ferritic to duplex to austenitic.
Duplex stainless steels, meaning those with a mixed microstructure of about equal properties of austenite and ferrite, have existed for nearly 80 years. The early grades were alloys of chromium, nickel, and molybdenum. The first wrought duplex stainless steels were produced in Sweden in 1930 and were used in the sulfite paper
industry. One of the major reasons, why duplex steel was needed in industrial applications, was the improved resistance to chloride stress corrosion cracking (SCC). The superior corrosion resistance results from the chromium content, especially in chloride stress corrosion cracking environments. In a particular environment, pitting corrosion sets in at a specific temperature for each stainless steel (corrosion visible after 24 hours). This temperature is called critical pitting temperature (CPT).
Duplex Applications
Striking characteristics of duplex steel are the high resistance to surface corrosion, local corrosion and stress corrosion cracking. The structure of this steel is particularly resistant to corrosion fatigue, energy absorption, erosion and abrasion, low thermal expansion and has good weldability. Due to its high resistance to general corrosion and surface corrosion, duplex steel is used primarily in the chemical industry, the petrochemical industry, desalination plants and in offshore technology.
ANDRITZ pumps are used in various positions in the seawater desalination process. Due to the aggressiveness
of the salt water, these pumps are made of a special, resistant material, namely duplex steel. The processing of duplex steel requires extensive practice and know-how. ANDRITZ has long-term experiences in the application of this special material. Depending on temperature and level of salinity, the pumps are either made of duplex or super duplex.
ANDRITZ high-pressure pump made of duplex steel.
How long can an ANDRITZ pump made of duplex stainless steel resist salt water?
The question of how long an ANDRITZ pump made of duplex stainless steel resists salt water is not as easy to answer as it may seem. In the first place, this depends very much on the salt water. The Baltic Sea, for example, has a very low salt content compared to the Persian Gulf (almost a factor of 4 is between them). Then the water temperature or operating temperature plays an important role. Every 10°C, the corrosion rate doubles. It is also crucial whether the pump is in continuous operation or in alternating operation. Continuous use is much better than an alternating one. In addition, the pH value has an influence. And last but not least, the additional contamination in the water is a factor that can change the corrosion resistance in both, positive or negative, directions. However, the biggest problem are not the parts that are in the water, but the transition zones, i.e. splash areas, where the wet and dry areas alternate. As a rule of thumb, one can say that super duplex is at least twice as good as duplex. It tolerates a temperature of about 20 to 30°C., 2 to 3 lower pH values and twice the chlorine content.