What if they could do something that had never been done before – install a new, bigger discharge system, but without replacing (or even moving) any of the rest of the equipment? It would save a lot of time and money, but still produce the desired final result: better and uniform fiber quality.
Improvements across the board
Uniform fiber quality with customized ANDRITZ digester
Anyone who operates an MDF plant today knows that raw material quality can be a challenge. Major MDF producer, EGGER, wanted to make sure that wouldn’t be a problem at its Bevern plant in Germany, so the firm asked ANDRITZ to install a custom-designed digester, to ensure great fiber quality for years to come.
As Johannes Mai, EGGER Bevern’s Project Leader, explains, “We weren’t getting up to the right temperature in the middle of the wood chips to soften the wood, so it could be refined properly. We were getting some shives and dust in the sheet. Jürgen Rose, Project Manager Recycling at EGGER Bevern adds, “Sometimes that could lead to sheet breaks. The digester had become a bottleneck, always running full, and the cooking time was too short.”
In this situation, many other companies would simply use more energy in the refiner, but that is not an option here. Bevern produces thin MDF sheets, mostly around 2-3 mm thick, which go to the group’s nearby coating plant in Marienmünster, to become panels for cupboards, drawers and shelves. As part of making this, Bevern operates a calender press, which is ideal for thin board. However, it also means that good fiber quality is absolutely vital, because web breaks can occur if the sheet is not strong enough. Therefore, EGGER decided to modernise, and they turned to ANDRITZ.
In this situation, many other companies would simply use more energy in the refiner, but that is not an option here. Bevern produces thin MDF sheets, mostly around 2-3 mm thick, which go to the group’s nearby coating plant in Marienmünster, to become panels for cupboards, drawers and shelves. As part of making this, Bevern operates a calender press, which is ideal for thin board. However, it also means that good fiber quality is absolutely vital, because web breaks can occur if the sheet is not strong enough. Therefore, EGGER decided to modernise, and they turned to ANDRITZ.
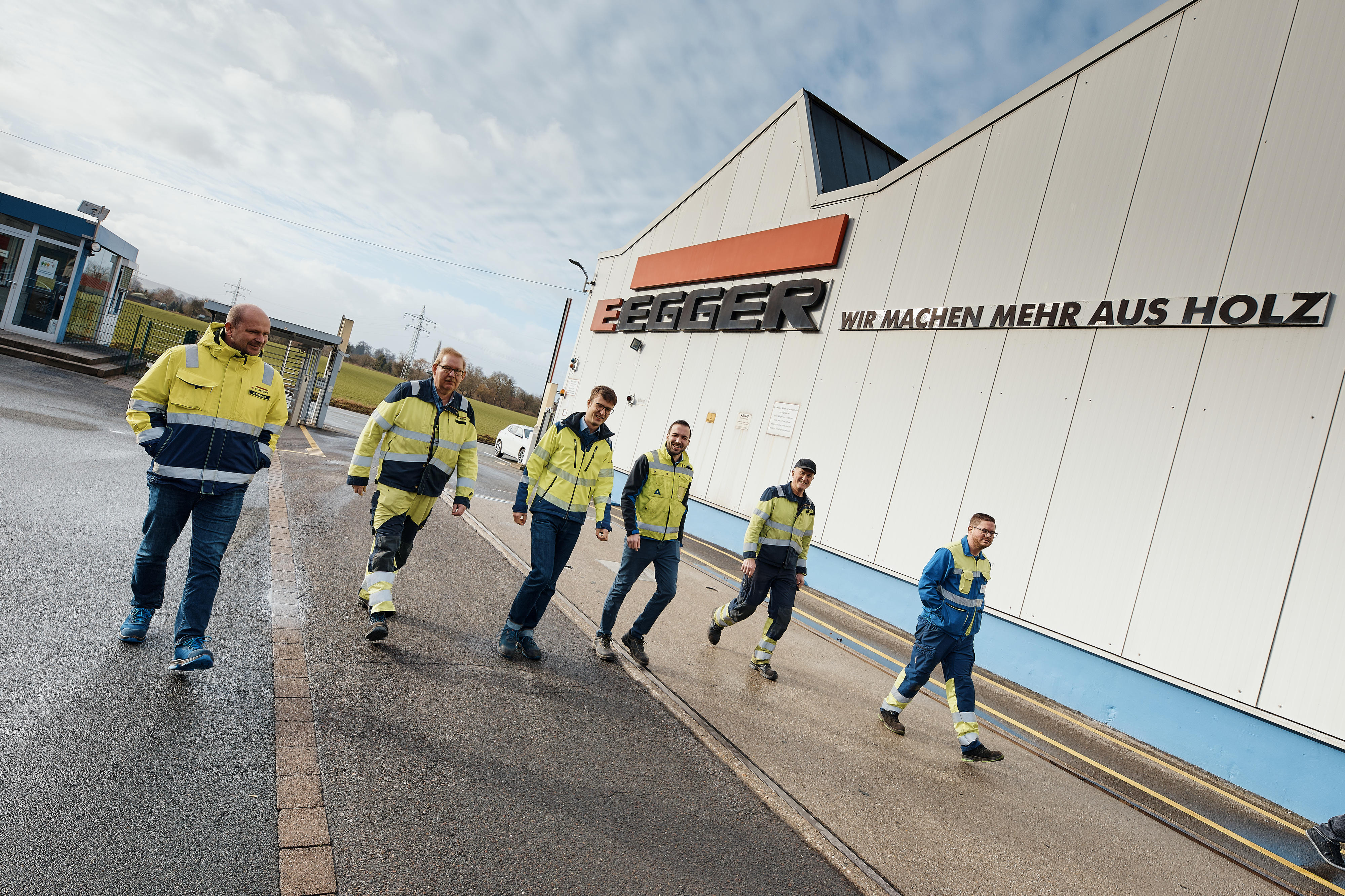
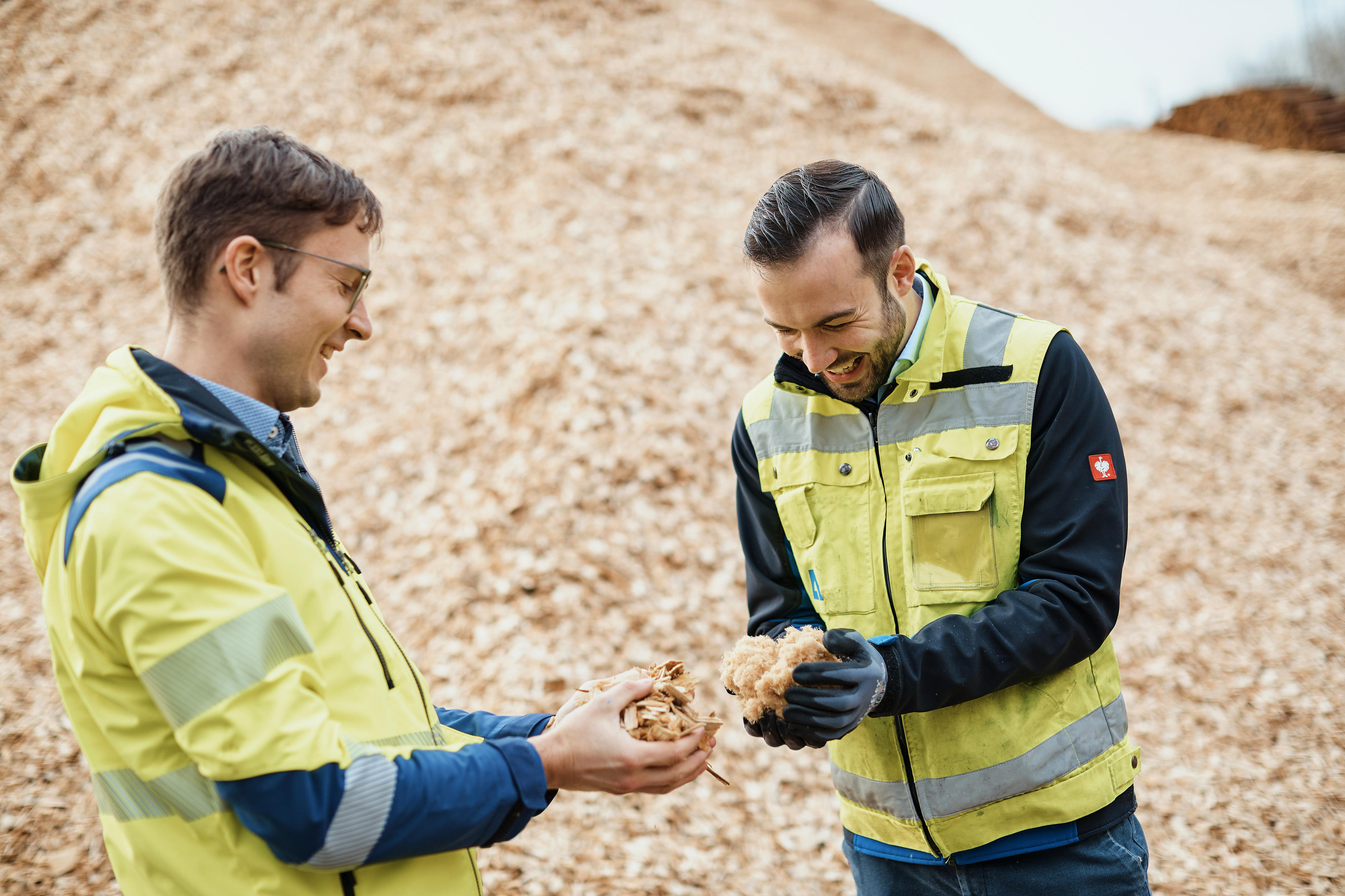
At the bottom, the discharge bottom agitator has been equipped with a newly developed chain drive with the gearbox and motor on the outside, which creates space and facilitates maintenance. The expanded digester volume also means that the plant can increase production, if other parts of the line are upgraded – which EGGER does plan to do. It could now also potentially use recycled wood, because the digester can cook drier wood for longer, which would mean additional cost and environmental benefits.
The answer – ANDRITZ redesigned the discharge system, creating a new shape that fits into the limited space available. For this highly-complex project, ANDRITZ also carried out an on-site plant audit, a 3D measurement of the existing plant, plus vibration & strength analyses of the existing digester foundation, to make absolutely sure it was all technically possible. At the top of the new digester, the shape was changed to a new eccentric design at the inlet, customized to fit the space available.
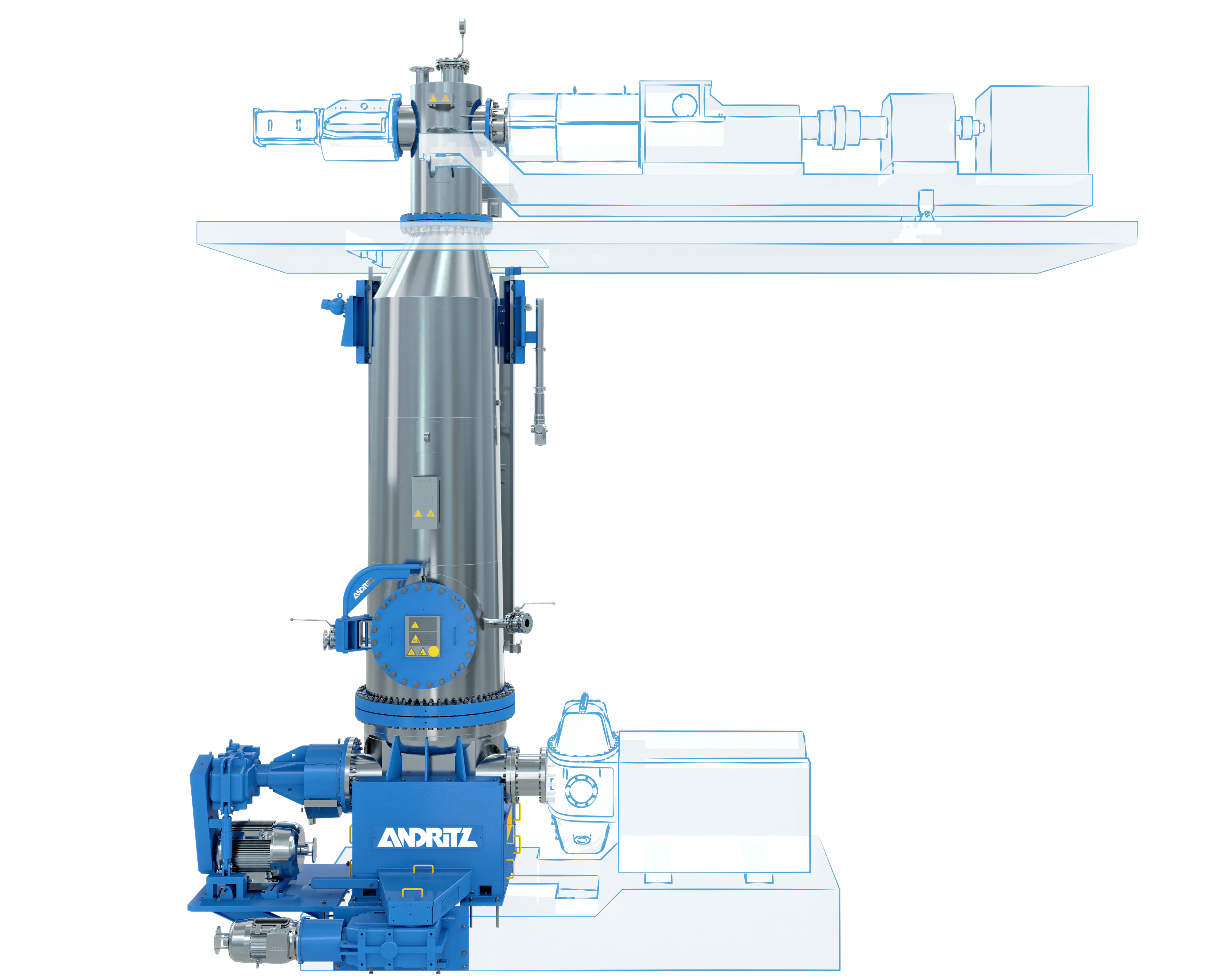
State-of-the-art technology.
Both of these innovations were world firsts in the MDF industry. The new discharge screw was supplied with the latest ANDRITZ Advaprotect 70 hardfacing to ensure highest lifetime. The discharge screw bearing unit has been equipped with ANDRITZ’s sleeve design, to ensure an easy exchange of the discharge screw, without a complete disassembling of the bearing unit.
The new, larger digester, with its state-of-the-art fill-level measurement system, also means that “EGGER now has the opportunity to experiment with different fill levels and cooking times,” explains Raphael Eichinger, Global Product Manager, Panelboard Service, ANDRITZ as it doesn’t constantly need to fill the digester completely to reach the plant’s production targets.