Valves - Lifetime safety and reliability
Valves have withstood the operating conditions within hydropower plants for more than a century and they fulfill various important tasks:
From safety elements in powerhouses or penstocks to tight sealing in waterways for maintenance purposes on hydraulic machinery.
Spherical valve for HPP Her decke: completion of tightness testing after service
In addition to butterfly and spherical valves described herein ANDRITZ HYDRO’s product range includes other valve types, like ring gates and cone valves.
Spherical valves are mainly used in high head applications, whereas butterfly valves are selected for the low to medium head range. Indicative design limits for each valve type are shown in the diagram above.
Both valves allow flow in both directions and fit perfectly for the use in the waterways of reversible pump turbines. They can be equipped with service and maintenance seals to allow significant reduction in plant downtime during maintenance.
Design
At the design stage, safety and functionality during operation come first. Analytical verifications are made based on customer requirements, and international standards (e.g. ASME), as well as ANDRITZ HYDRO internal instructions. Modern ANDRITZ HYDRO valves offer numerous innovative technical features, which appeal to customers.
Among other features , ANDRITZ HYDRO now offers an auto-oscillation (self-excited pressure pulsation with increasing amplitudes, which can lead to penstock rupture) detection device. By opening or closing of the maintenance seal the oscillating system is de-tuned and damages due to auto-oscillation can be prevented. This function can either be performed fully automatically or manually after an alarm.
Recently, the design of the butterfly main inlet valve for HPP Cerro del Águila in Peru (DN 3150 mm/PN 36 bar) was completed. In this high pressure application ANDRITZ HYDRO achieved a substantial reduction in the valve head losses of approximately 15%. This could be managed after several optimization loops by the utilization of CFD (Computational Fluid Dynamics) calculation programs and by taking existing model test results from the standard valve disc geometry as a basis.
Furthermore, this design features leakage monitoring of the maintenance seal, which allows operators to check its tightness before dismantling, thus increasing safety for maintenance staff.
The spherical valve for HPP Teesta Urja in India (DN 1,900 mm/PN 90 bar) is exposed to high concentrations of aggressive sediments in the river water and consequently subject to erosion damage. Therefore essential components of the service and maintenance seals were furnished with a tungstencarbide coating, which ensures a significant extension of the maintenance interval.
Exploded view: main components of butterfly valve
Manufacturing, installation and commissioning
Nominated ANDRITZ HYDRO technical competence centers for spherical and butterfly valves are located in Ravensburg, Germany and Linz, Austria. The strictest requirements are enforced concerning material and fabrication quality as well as machining tolerances during the manufacturing process.
Main components can be made either from castings, forged or welded structures based on size and pressure rating criteria.
Modern narrow gap welding techniques (e.g. submerged arc or electron beam) are applied on thick walled items to ensure competitive manufacturing costs. These reduce the required quantity of filler material and, incidentally, minimize welding distortions too.
Functionality of single components as well as the overall system are checked during workshop assembly (including pressure and tightness tests) to ensure smooth installation of the valves at site.
Commissioning ensures the correct setup and optimization of operational parameters, for example tuning of the valve closing times to prevent unacceptable penstock water hammer.
Service
Valves are exposed to high loads during operation but the years of operation are less critical than the effective number of load changes. Nowadays hydraulic machinery and their valves are subject to an increased number of start/stop cycles due to changes in the grid demands, however their layout and design was calculated for far fewer cycles. Therefore valve maintenance and rehabilitation are becoming even more essential to guarantee both the operational safety and the availability of the entire hydropower plant.
Condition assessments of important components and design improvements can be made in cooperation with customers in a pre-service phase to optimize the rehabilitation and its duration. For example, at the total overhaul of the spherical valves at HPP Herdecke in Germany (DN 3,300 mm/PN 28 bar/170 tons), where all components had to undergo non-destructive testing and documentation. Wear and defective areas were assessed referring to functional safety and rectification measures, which were discussed and defined with the customer. Following the completion of the overhaul and the valve re-assembly, final tightness and functional tests were immediately performed in the workshop, whereupon a “drop-tight” rating could be reached.
With this valve service our customer can rely on safe and undisturbed operation in the upcoming years.
The global ANDRITZ HYDRO valve fleet covers more than 3,500 installed units. Due to one century of valve experience in combination with constant research and development efforts, every size, pressure rating and technical challenge can be managed individually, be it for new applications or service tasks.
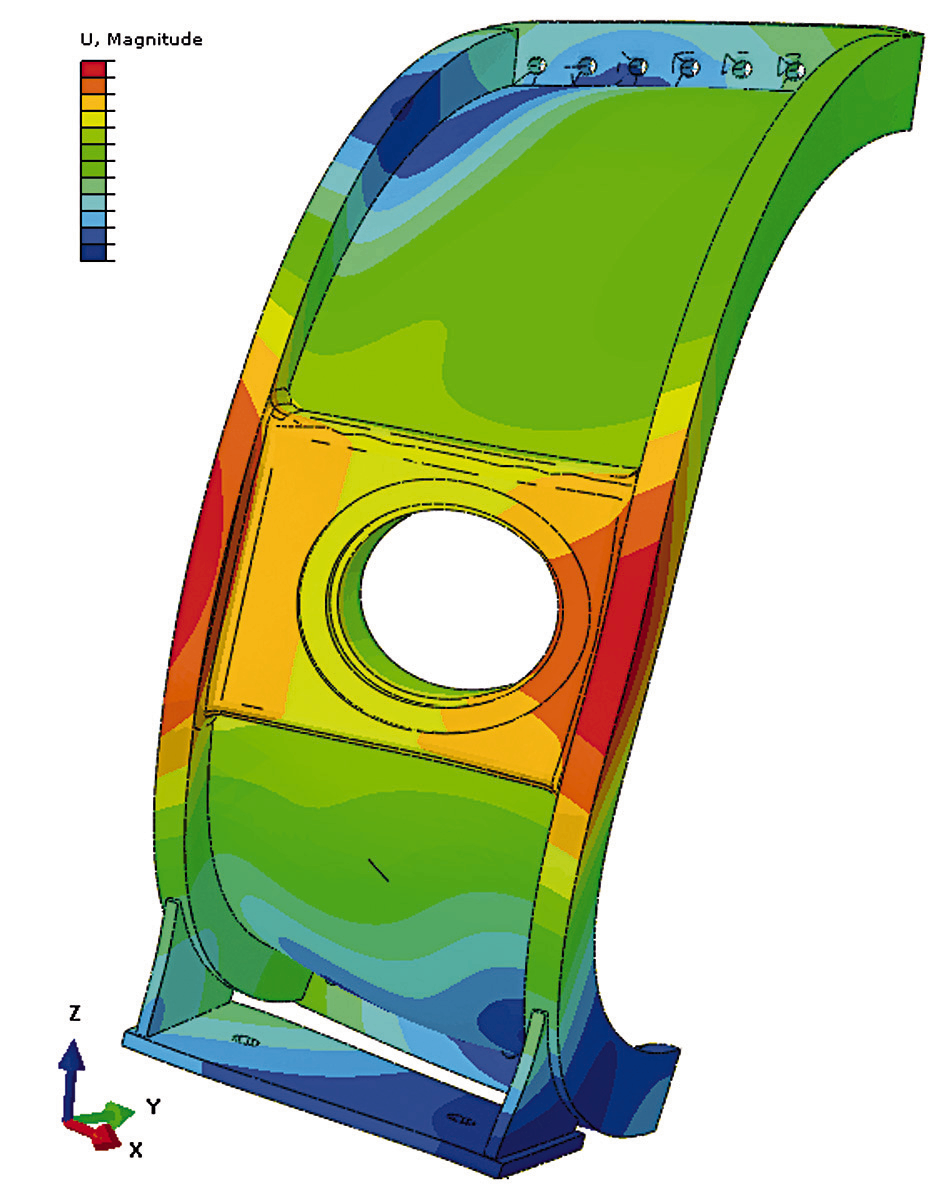
Finite element analysis plot for stress and deformation verification.
TECHNICAL DATA
Projects currently under execution:
Cerro del Águila: | |
3 butterfly valves | |
Nominal diameter: | 3,150 mm |
Design pressure: | 36 bar |
Nant de Drance: | |
2 butterfly valves | |
Nominal diameter: | 6,000mm |
Design pressure: | 10 bar |
Upper Tamakoshi: | |
1 spherical valve | |
Nominal diameter: | 2,500 mm |
Design pressure: | 90 bar |
Teesta Urja: | |
6 spherical valves | |
Nominal diameter: | 1,900 mm |
Design pressure: | 89.3 bar |