STEP BY STEP
CHALLENGE
CO2 IS PRODUCED WHEN FOSSIL FUELS ARE BURNED.
This accelerates climate change and causes enormous environmental pollution.
SOLUTION
6.3 MILLION LITERS OF BIOMETHANOL
Swedish company Södra has the capacity to produce up to 6.3 million liters of commercial-quality biomethanol a year with help from ANDRITZ. This biomethanol is used to make biodiesel, which can be used as an alternative fuel source for motor vehicles.
Paper and board are much in demand – around 400 million tons of different grades are produced worldwide every year from mechanical and chemical pulp. In order to meet the demand and still conserve resources, many companies are searching for efficient technologies and strategies. In view of this, ANDRITZ has launched the “CircleToZero” initiative.
Up to 750,000 tons of pulp and 6.3 million liters of biomethanol are produced annually at the Södra mill in Mönsterås.
© Södra“We take a holistic look at all of the chemical loops in pulp production within a mill to see where we can use, recycle or refine side streams to make new products,” says Lauri Pehu-Lehtonen, director of the research and development team in the ANDRITZ Recovery and Power division. “With the technical approach of the CircleToZero initiative, we would like to help our customers reduce chemical consumption, produce less waste and emissions, and tap new sources of income.”
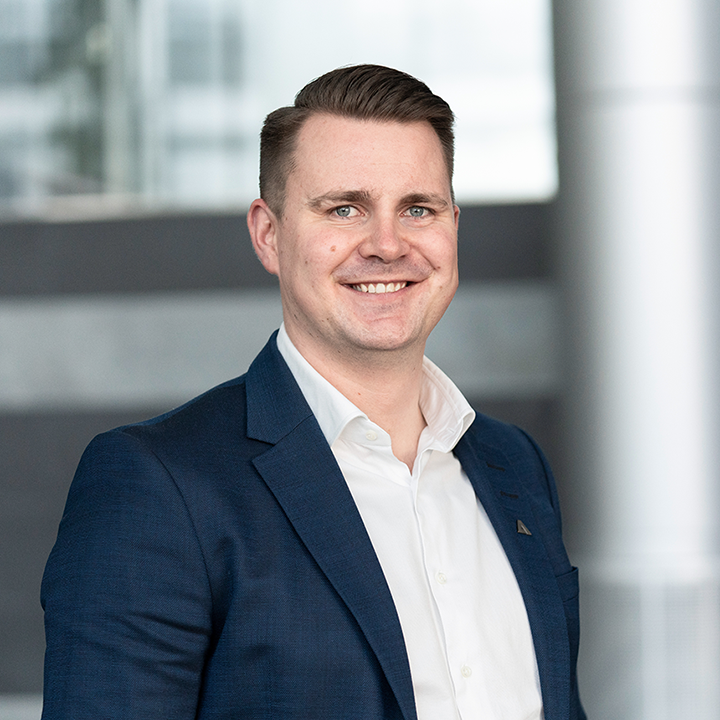
CircleToZero
“CircleToZero” means analyzing all the chemical loops in pulp production to see whether side streams can be used, recycled or refined to make new products.
Many years of successful work together unite ANDRITZ and Södra.
© SödraSödra’s pulp mill in Mönsterås is a case in point. The ultra-modern mill produces up to 750,000 tons of pulp a year from softwood and hardwood in addition to district heating and also tall oil that is converted into biodiesel. Furthermore, the mill has been producing raw methanol here and then refining and selling it as high-end biomethanol since 2020 – and this is unique worldwide so far.
The plant designed, supplied and built by ANDRITZ has the capacity to produce 6.3 million liters of biomethanol annually, which Södra sells to biofuel producers. It is used there as a CO2-neutral substitute for fossil methanol in the production of biodiesel, which can be used in turn as fuel for maritime vessels, a use that EU legislation promotes and supports financially in order to achieve the ambitious emission-reducing targets in the transport sector in coming decades.
CERTIFIED SUSTAINABILITY
Södra’s biomethanol provides uniquely high greenhouse gas savings. From a lifecycle perspective, the product can lower emissions by well above 95% compared to fossil alternatives. The product is certified according to the ISCC process. This means that its production process is ecologically, socially and economically sustainable. Around 70% of Södra’s members have FSC® and/or PEFC™ certification. Both certificates make extensive demands on sustainability, environmental compatibility of forest management, the quality of work, and the social competency of the forestry companies.
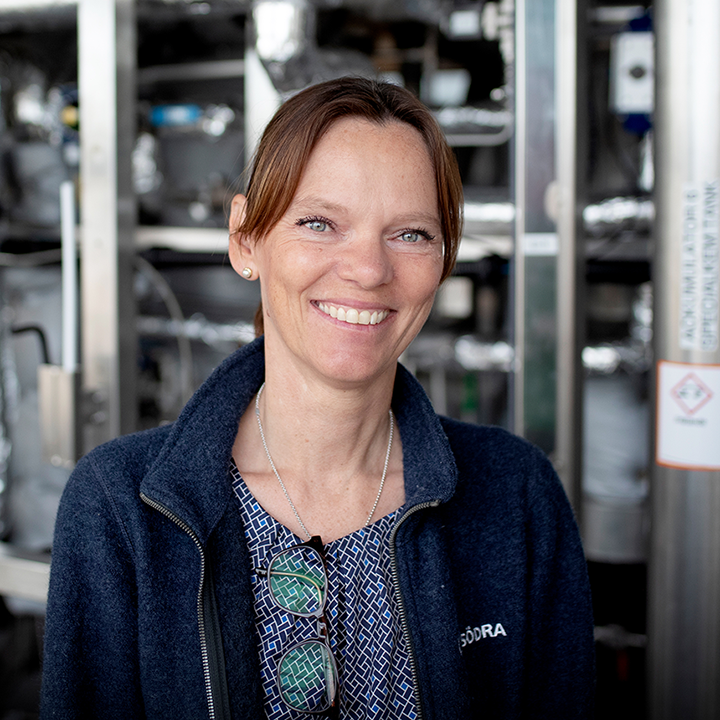
"For this, you need the right spirit, support from the top management, know-how, and perseverance."
Catrin Gustavsson,
Business Area Manager for Innovation at Södra
“The raw material for our biomethanol comes from the sustainably managed forests of our members – more than 50,000 Swedish forest owners,” reports Catrin Gustavsson, who is business area manager for innovation at Södra. “We are convinced that the most efficient and most successful projects pop up when sustainability and economy are attached equal importance.” Making use of side streams and by-products in pulp production is a very promising strategy. For, ultimately, Södra wants to extract as much as possible from the precious commodity that is wood – in the interests of the environment and of all stakeholders. “It is important to define this as the objective and then start to optimize plant and production operations step by step. For this, you need the right spirit, support from the top management, know-how, and perseverance.”
The key: teamwork
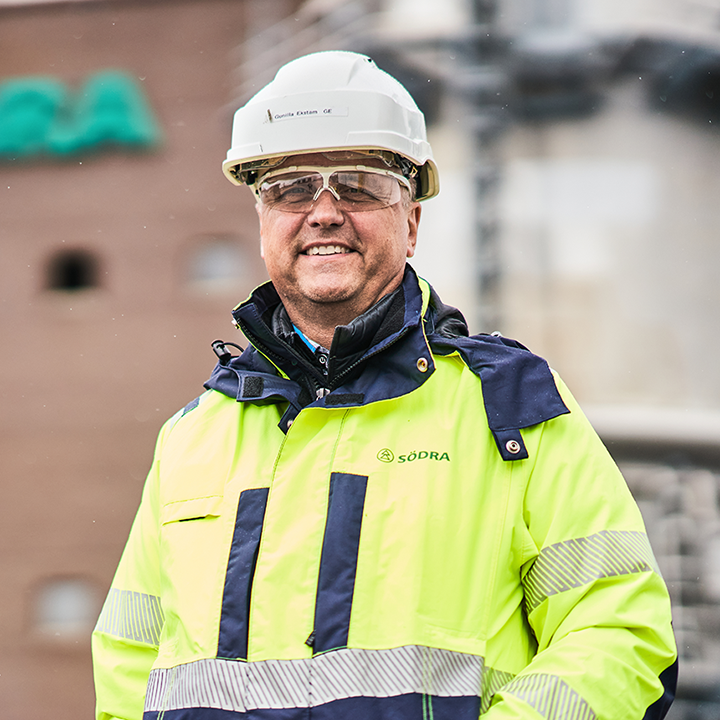
"We were breaking new GROUND."
Christer Thörn,
Director of the Södra mill in Mönsterås
Christer Thörn, director of the state-of-the-art mill in Mönsterås, confirms this and underlines that there are constant technical and operating challenges to be tackled. “Different products are produced in the pulp mill, and if there are delays or stoppages there, we have to adjust the production of biomethanol accordingly,” he says. His staff of over 400 had to be willing to learn something new every day when it came to improving volume, quality and performance. As technology supplier and adviser in production operations, ANDRITZ played an important role. “By scaling the process up to industrial level, we were breaking new ground. To do this, you need a diversified team with a wide range of skills. You only find the right solutions if you work together,” says Thörn.
One of Södra’s advantages is that the biomethanol is categorized and certified as “a product made from forest residues” – an attractive description when you are looking to be climate-neutral. “This doesn’t just apply to the transport sector,” says Catrin Gustavsson. “We will also offer our biomethanol as a base material for the chemical industry.” There are many sales opportunities. After all, around 100 million tons of methanol are traded worldwide every year. The demand for “green products” is rising in many sectors, the sustainability expert underlines, and Södra will take part in this trend: “We will continue to optimize production in Mönsterås, investigate use of the process in other mills and, at the same time, sound out any new commercial opportunities.”
This is an approach that coincides with ANDRITZ’s goals and plans. “In addition to biomethanol, we can also produce first-class, commercial-grade lignin and sulfuric acid with our CircleToZero solutions,” says ANDRITZ expert Pehu-Lehtonen. The Brazilian paper and board producer Klabin, for example, has started doing exactly this. At its mill in Ortigueira, southern Brazil, sulfurous gases that are normally burned in the boilers or lime kiln are used to produce sulfuric acid. The results are substantial savings on chemicals, including sulfuric acid, and much lower consumption of sodium make-up chemicals. In Pehu-Lehtonen’s view, this is by no means the end of the story. “We have a few more ideas on how to improve the efficiency and climate balance of pulp mills within the scope of the CircleToZero initiative in the future.”
TALKING TECH: PRODUCTION OF BIOMETHANOL
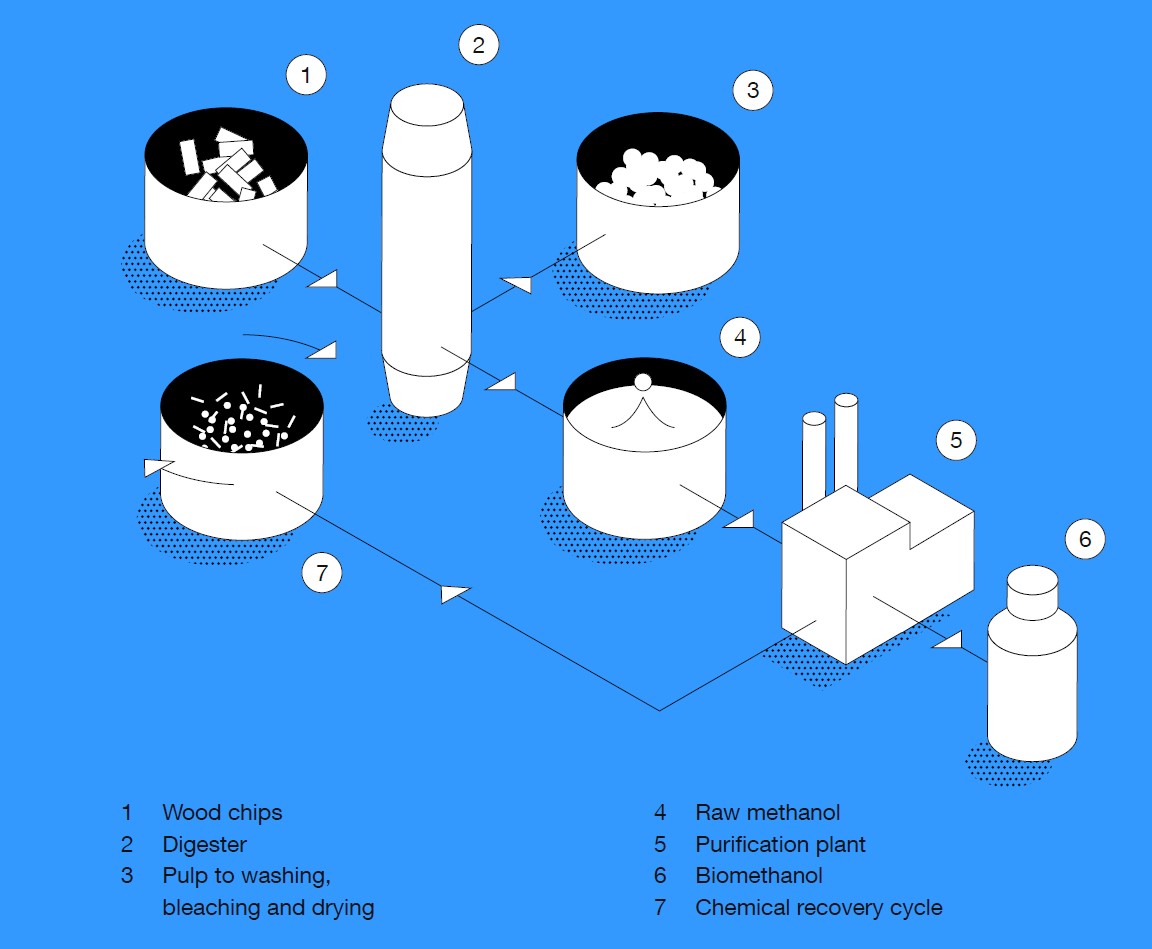
Wood chips are cooked together with chemicals to break the wood down into its component parts, i.e. cellulose and hemi-cellulose (pulp), and lignin. Next, the chemicals, lignin and other residues are washed out of the pulp. They form a black liquor whose water content is then reduced by means of evaporation. What remains is a condensate of methanol, turpentine and sulfur compounds.This condensate is purified so that it can be reused in the mill. Raw methanol is formed – a mixture of combustible residues. Normally, the raw methanol is burned to generate heat and energy. Thanks to a patented extraction process, Södra can produce commercial-quality biomethanol. For every ton of pulp that leaves the mill, some 10 kilograms of biomethanol are produced.