Hydraulic Laboratory Vevey
Many years of experience in the development of hydraulic machines
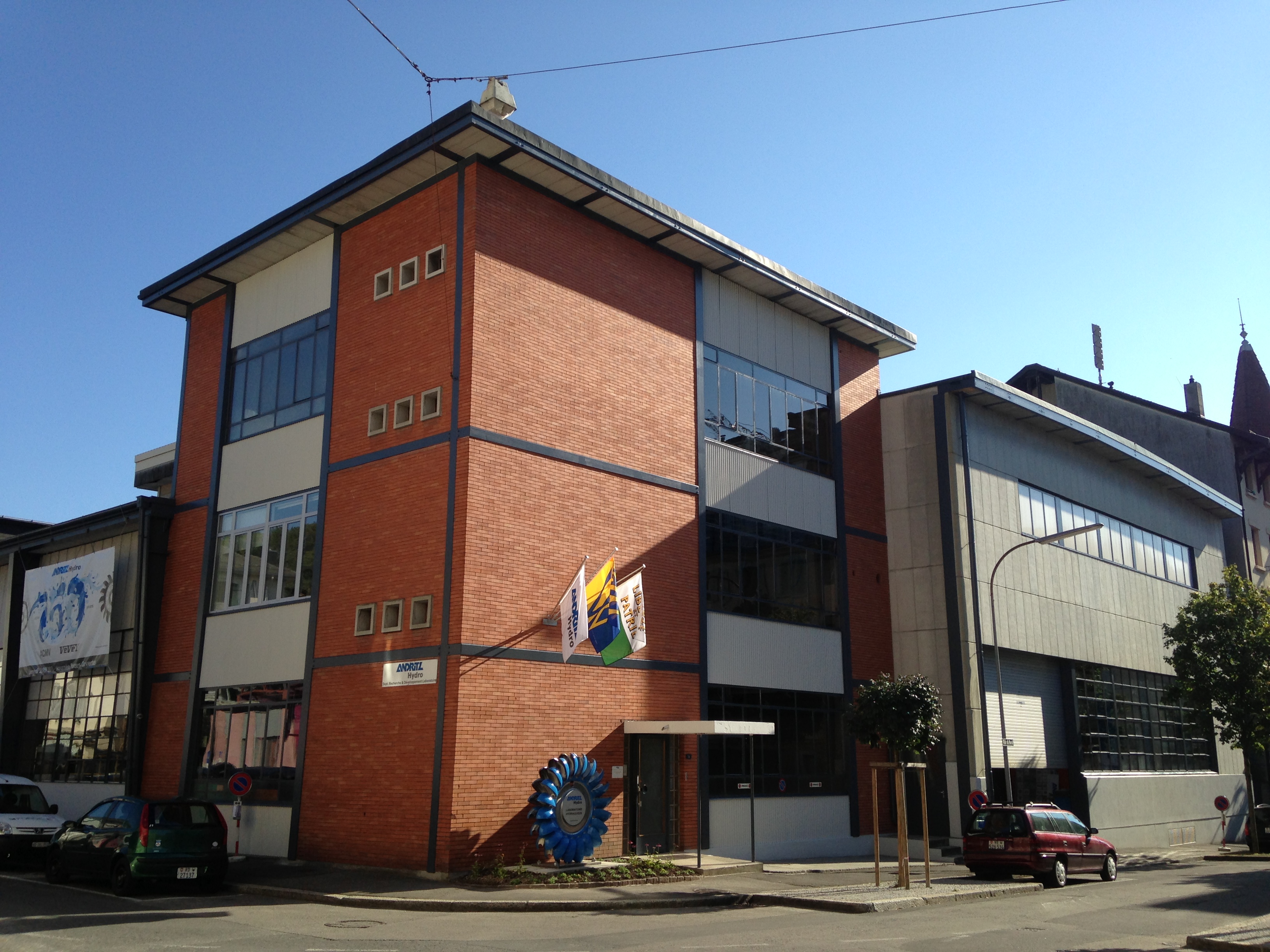
History
- Built in 1919 as the first hydraulic laboratory of the Ateliers de Constructions Mécaniques de Vevey
- The present building was inaugurated in 1959 and extended in 1978 to keep pace with market developments
- 2005: installation of an independent Pelton horizontal test rig and upgrade of the pumping system on the universal test rig
- 2017-2018: installation and commissioning of a vertical axis Pelton test rig
- Addition of cavitation generation and cavitation erosion test rigs in 2016 and 2018
Test rigs
- 3 test rigs for Pelton models; horizontal or vertical axis
- 1 test rig for the study of hydro-abrasive erosion
- 1 test rig for the study of cavitation
- 1 universal test rig, currently inactive
Hydraulic design
A key element in layout optimisation
Today's technological challenges can be met through the optimal integration of all our development resources.
The design of reliable high-performance, hydraulic machines adapted to new production requirements need the use of sophisticated computerised methods. The development of these machines, integrating know-how and experience, is carried out by a computer system using the latest CAD (Computer Aided Design), CFD (Computational Fluid Dynamics) and FEA (Finite Element Analysis) tools, allowing thus an accurate and detailed evaluation of flows and structures. Laboratory tests provide the necessary data to update the analysis tools, final machine optimisation and performance monitoring.
Specialised software is used to develop the hydraulic profile of each turbine component.
The geometry thus mathematically produced by a CAD system is the starting point for the subsequent evaluation and manufacturing of the model.
The numerical models used to evaluate this geometry are implemented in flow (2D, 3D) and structural (CFD, FEA) simulation software.
Model tests
An indispensable complement to digital simulation
Even though the methods of numerical flow simulation are constantly improving, ANDRITZ continues to invest in the development of modern test facilities.
In addition to the role played by the final optimisation, laboratory tests allow the verification of guaranteed performances according to IEC standard 60193 and a complete analysis of the behaviour in all operating areas, including transient regimes.
In addition, they remain an indispensable tool for the validation of numerical simulations.
Thus, taking into account the different types of turbines, the following test rigs are available for model tests:
- Test rig for vertical axis Pelton turbines
- Test rig for horizontal axis Pelton turbines
- Universal test rig for Francis, Kaplan, pump-turbines and storage pumps
On-site tests
Performance measurement of industrial hydraulic machines
In application of international standards, IEC publication 60041, ANDRITZ carries out acceptance tests on industrial machines in order to check the guaranteed performances and to study the behaviour of the machines.
The team in Vevey is more particularly specialised in thermodynamic measurements applied to Pelton turbines.
Absolute measurements by means of the thermodynamic method
Energy losses of a hydraulic machine cause the water to heat up. The losses, and therefore the efficiency, can be determined by measuring the temperature rise of the water between the turbine inlet and outlet.
Index measurements
They are used to:
- determine operating characteristics expressed as relative values of power, flow and efficiency
- verify the power guarantee
- obtain information on the operation of the turbine, e.g. for monitoring purposes