The kappa variable is one of the most important for the complete pulp process. The quality of this variable in the digester discharge impacts every process that follows. The greater the stability of the kappa, the less variability of the entire fiber line, which has repercussions on quality, yield and chemical consumption.
Data analysis and advanced controls to generate digester kappa stability
Working with ANDRITZ, Suzano mill reduces their chemical consumption and achieve greater quality and yield
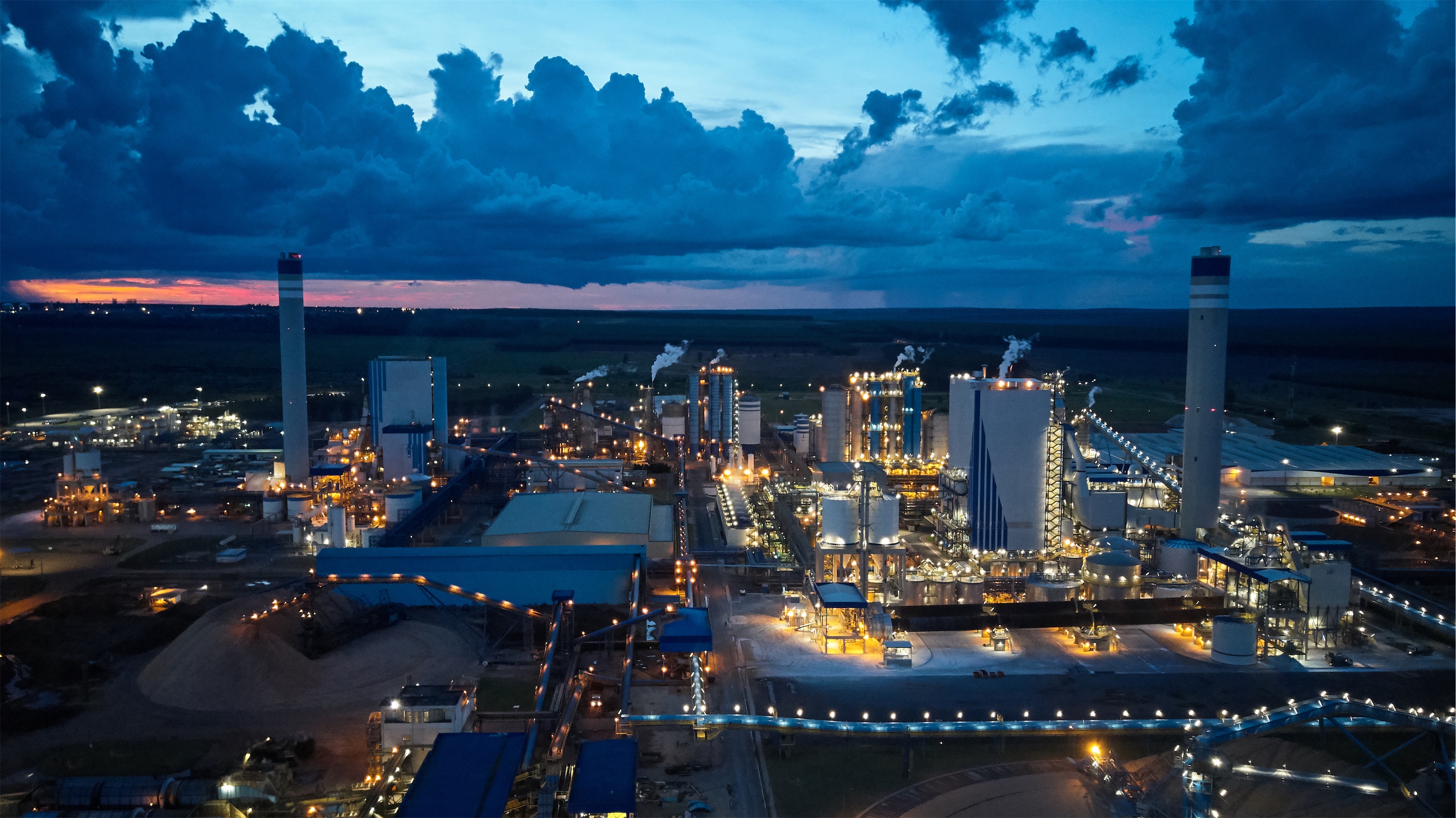
A project carried out in partnership with Suzano at the Três Lagoas, located in the municipality of Três Lagoas in Mato Grosso do Sul. The mill used advanced controls to obtain a low standard deviation of the kappa and, consequently, an increase in kappa, an increase in pulping yield and a reduction in alkali charge.
Two applications from the Metris All-in-One platform were integrated to gather a variety of data and perform data analysis. The Metris Product Tracker dealt with different retention times between the analyzed variables, while Metris Machine Learning performed semi-supervised clustering. For advanced process control, the model-based controller (MPC) from the ANDRITZ control library was used.
The kappa number and the pulp cooking process
The kappa number is one of the main variables in the pulp cooking process. A more stable kappa means better pulp quality and higher fiber line productivity. “Controlling the kappa at the digester discharge, with all the variability of the wood, has always been a challenge,” comments Álvaro Costa, Executive Manager of Suzano's pulp production. Prior to working with ANDRITZ, all temperature and chemical load adjustments were performed manually by operators at the Três Lagoas mill.
During a benchmarking meeting between Suzano mills, the Jacareí mill shared that they had recently completed a project that enabled them to quickly advance their control strategy and automate all variables in this process.
“Within the Suzano group there was a successful case of work on the digester in Suzano Jacareí. Adriano Ramos, Specialist from the ANDRITZ Automation and Digitalization team, conducted [the project] with the support of the client's team and achieved excellent results. The people from Suzano Três Lagoas contacted the team from Jacareí and asked ANDRITZ to do the same work there," explains Arthur Santos and Gustavo Ogura, Automation and Digitalization specialist at ANDRITZ.
The first step was to review the entire process that was implemented at Jacareí and determine how to replicate it at Três Lagoas. Because not all factories are identical, this meant that the team’s first challenge was to adapt the Jacareí initiative to the unique conditions at Três Lagoas.
The work to automate Kappa control
The project started in August 2020, when the teams began reviewing the digester controls, starting with the adjustment of the H-Factor control (the temperature control of the cooking zone). Adjustments were made and to the existing control and new conditions were added to the logic.
Costa explains that there were three main conditions required to automate kappa control. First, a feedforward density control was set to stabilize the digester level. In parallel, physical modifications were made to the residual alkali measurements, which made it possible to automate the alkaline charge dosage in the cooking steps.
“Finally, we closed the circuit through the automatic control of the kappa by temperature (H-Factor). Several other systems were also improved, such as discharge control and production ramps, among others, thus ensuring the success of the application,” concludes the Executive Manager.
After the general shutdown, which took place at the beginning of December 2020, all controls were switched on and, as of January 2021, the benefits started to become apparent. With a more stable kappa, the project achieved better efficiency in the delignification area. As a result, pulp quality became more stable and chemical consumption was reduced.
Industry 4.0, advanced controls and operational knowledge
In Costa's assessment, all critical processes need quick and accurate responses when the focus is on Industry 4.0. “What we did in this project was use all our operational knowledge to build an adaptive mathematical model that could automatically control, without human intervention, one of the main variables in the pulp production process.”
One of the most interesting results of the project was that the Três Lagoas mill achieved the lowest standard deviation of the entire Suzano group. In this regard, Costa points out that the project allowed for much more stable operation of the digesters. “As a result of this stability, we have the lowest 2 sigma kappa standard deviation of the entire Suzano group, and, I dare say the pulp market, with average values below 0.20 points at the mill 1 and 0.4 points at mill 2.”
Santos and Ogura recall that carrying out the project also brought comfort and confidence to the operators. “With advanced controls taking care of the process, operators can better manage their area. Usually, they take care of more than one area and many pieces of equipment,” add the ANDRITZ experts.
Perspectives created through teamwork
Despite the positive results, the team continued to look for additional improvements. Costa remembers that, during the project, they saw an opportunity to connect two initiatives. “One was the kappa control developed and applied in both mills. And the other was a pilot project called ‘Rocket,’ linked to the wood supply strategy at the mill,” he explains. The team is now working on Phase 2, the integration of these projects, with a focus on further improving the stability of the digesters.
In the words of Suzano's Executive Manager, besides improving the process yield, Suzano’s work with ANDRITZ contributed to lower consumption of chemicals, increased stability, and improved quality of the final product.
“Certainly, the project has been fundamental in advancing the stability of the digester, delignification and bleaching areas,” says Costa. “Considering that Phase 1 of this project is complete and that we are integrating two projects with a vision of optimized control, it will certainly be an innovative leap forward, given the potential of these tools.”
Machine Learning and Product Tracker are Metris Plant InSights solutions.
Learn more by accessing Automation Solution Finder.
Gustavo Ogura, Automation and Digitalization specialist at ANDRITZ
Arthur Santos, Automation and Digitalization specialist at ANDRITZ
Find out more ...
Contact us!
Metris - ANDRITZ Digital Solutions
Headquarters, Austria
E-mail: metris@andritz.com
CONTACT US