Microcrystalline cellulose (MCC) is purified and partially depolymerized cellulose obtained by treating alpha cellulose with mineral acids. It was originally developed in the 1950s in a search for a stronger rayon thread. Unfortunately, high production costs have restricted its use for decades, and although it is widely used in many applications in a variety of industries, the high cost is still a significant hindrance for potential users.
A-ConCrystal™ continuous process technology for microcrystalline cellulose
Value-added bio-products from pulp
Microcrystalline cellulose – or MCC for short – is widely used for many purposes in a variety of industries, currently most known from the pharmaceutical and food sector. To date, the production of MCC has been limited to relatively small production plants operating with batch process. ANDRITZ A-ConCrystal™ continuous process MCC technology allows cost-effective, high-capacity production either as standalone production plant, or – with remarkable synergy benefits – when integrated into an existing industrial platform, such as a pulp mill. This novel process technology has several features that offer many new possibilities for the use of MCC in different application areas.
Technological advantages with A-ConCrystal™
- Easy-to-control process conditions
- Flexibility to use different raw materials
- Shorter retention times than with conventional methods
- Extremely efficient mixing of chemicals
- Stable quality and high yield
ANDRITZ A-ConCrystal™
The technology behind the A-ConCrystal™ process was developed at Aalto University in Finland. ANDRITZ has licensed the technology to implement it at full mill scale and commercialize it for the global market. Compared to the conventional production methods, the core of the A-ConCrystal process is in the unique mixing efficiency of the process chemicals and higher process temperatures. This leads to shorter retention times, lower chemical consumption, and environmentally friendly production. This novel technology keeps the costs at a much lower level and makes large-scale production economically viable.
One of its key features is that, unlike the traditional methods based on batch processing, the A-ConCrystal process is continuous. ANDRITZ has developed continuous process technology for wood pulping for several decades, and now this technology has been adapted for MCC manufacturing. It makes the process easy to control during the production, which in turn ensures high product quality throughout the process – the end product has been proven to fulfill pharmaceutical standards in tests conducted by an internationally recognized, independent test laboratory.
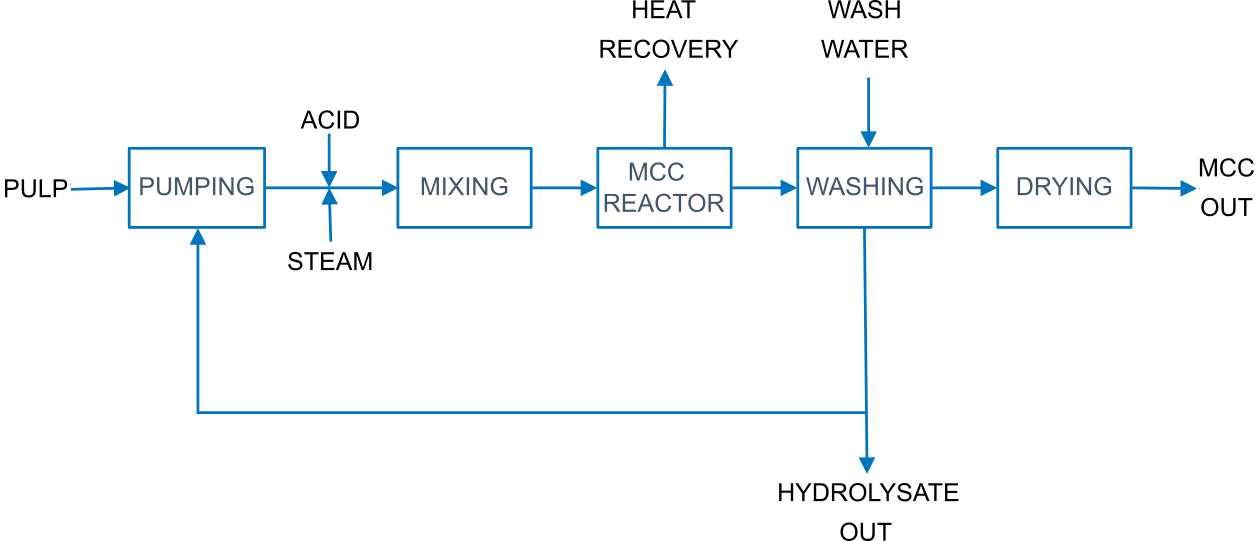
A-ConCrystal™ process
I have evaluated A-ConCrystal continuous MCC-manufacturing technology and compared it to conventional batch technology. Novel A-ConCrystal continuous process with unique chemical mixing and heating solutions takes MCC-manufacturing to modern process technology level. Efficient mixing and adjustable hydrolysis conditions ensure very stable MCC quality.
I am happy that ANDRITZ has taken the challenge to develop MCC-production technology!
— Jorge Wilson Freire, Senior Technical Consultant
Pulp mill integration
A unique capability of the ANDRITZ A-ConCrystal technology is the ability to be integrated into an existing industrial platform, for example into an existing pulp mill. With the synergy advantages offered by this type of integration, high production capacities are possible with low capital expenditure and operating expenses. Integrating the technology into a pulp mill provides a platform that is self-sufficient in energy, unlike the previous production processes. The generated hydrolysate can be processed in either the mill's chemical recovery plant or in effluent treatment. It is also possible to use the hydrolysate to produce other bio-based chemicals, such as different sugars and ethanol.
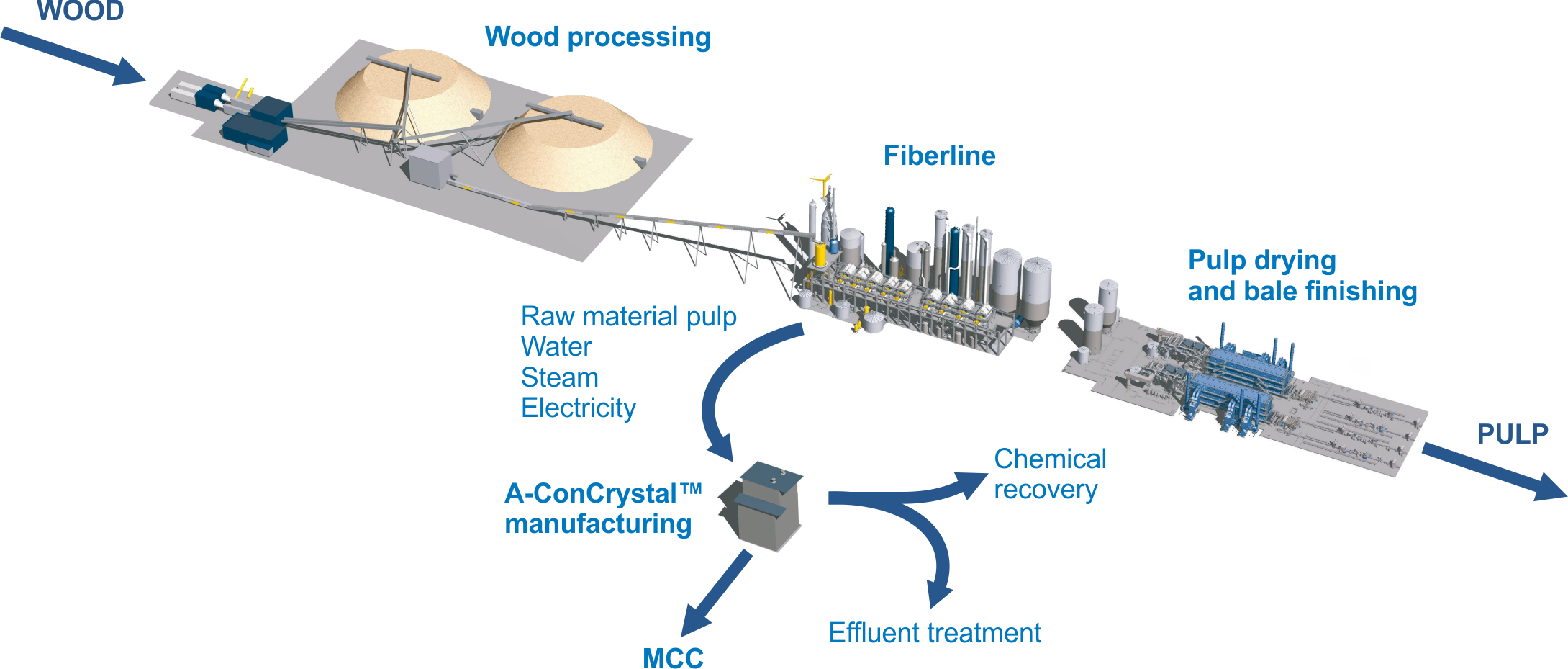
The A-ConCrystal™ plant can be integrated easily into a pulp mill to achieve remarkable synergy benefits.
Flexibility in raw materials
A-ConCrystal process technology is also flexible in terms of raw materials – it can handle all commercially sold pulps, including dissolving or paper-grade pulp. The technology also makes it possible to produce special MCC varieties from unbleached pulp – so called brown MCC – which opens up new possibilities in applications that would not require a high brightness product.
Proven technological solutions
A-ConCrystal continuous process microcrystalline cellulose technology utilizes ANDRITZ medium-consistency technology that has been thoroughly tried and tested in pulp mills around the world. When this technology is adapted to produce MCC, it guarantees extremely efficient mixing of chemicals, maximal reactor utilization, stable operation throughout the process, and increased yield.
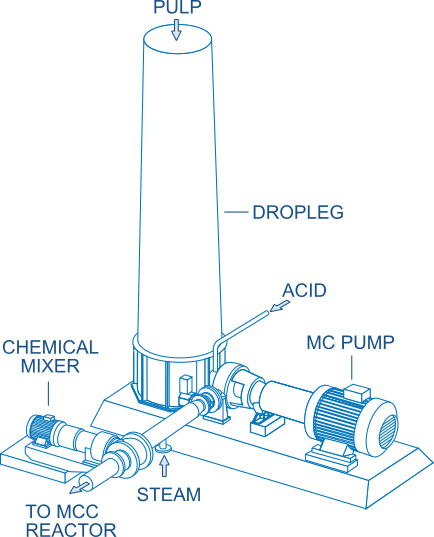
Ensuring efficient chemical mixing with technology adapted from pulp production
ANDRITZ A-ConCrystal™ technology can be used to make a variety of MCC products from different raw materials
Commitment to sustainability
Commitment to environmental protection and to reducing the impact of climate change is at the core of ANDRITZ sustainable technology solutions. The positive impact of decreased chemical consumption and reduced energy usage of A-ConCrystal continuous process technology on the production of microcrystalline cellulose is one step on this path, and reductions to greenhouse gases another.
We have measured the global warming potential of our technology by evaluating the CO2 equivalents (kg CO2/ton of MCC) in two different scenarios, compared to traditional MCC production – standalone and integrated into an existing industrial platform. In both cases A-ConCrystal process technology resulted in lower CO2 equivalent emissions, and in the case of an integrated plant the reduction was up to 24%.
New market opportunities
Even though pharmaceutical and food applications are dominating the MCC market at the moment, with the low production costs and high capacities made possible by the ANDRITZ A-ConCrystal technology, it is expected that new markets for MCC will open up where the high costs associated with previous production methods made it unviable. Opportunities are seen – for example – in industrial composites, animal feed additives, polymer and paint industries, and in the cosmetics sector.