Innovative carbon capture technology for a sustainable future
Carbon Capture, Utilization, and Storage (CCUS) can make an important contribution to the urgently needed reduction of greenhouse gas emissions. ANDRITZ has various types of solutions in its portfolio that help customers to remove CO₂ from their flue gases which can be stored, or processed for further use in making other products.
For more than 15 years, ANDRITZ has been active in the field of decarbonization of flue gases in different industries. The CCUS solutions developed have been tested in cooperation with various universities and scientific entities. The first approach was the development of solutions for the fossil fueled power sector, where ANDRITZ has installed and tested pilot plants for nearly 10 years.
Meanwhile, ANDRITZ is also active in the cement, pulp & paper, waste to energy, iron and steel industries, as well as the maritime industry. The latest reference of a CCUS solution was recently installed in the German cement industry. The Global Cement and Concrete Association (GCCA) reports that the cement industry contributes around 7 - 8% of global man-made CO₂ emissions. That means curbing the CO₂ emissions resulting from cement production will make a crucial difference in helping the world achieve its net-zero objectives to limit global temperature rise. ANDRITZ is set to play a key role in helping the cement industry achieve this target by deploying its CCUS technology that is already proven in other industries.
In this pioneering project, ANDRITZ was the engineering, procurement, and construction (EPC) contractor for a demonstration project to develop Europe’s first carbon capture plant in the cement industry. The plant has been constructed for Rohrdorfer Zement at its Rohrdorf site, near Rosenheim in Germany. This site was already a focus for major developments in decarbonization. In fact, in 2022 it was producing cement with 45% less CO₂ than in 1990 by optimizing cement types and fuel use. This approach can achieve a maximum reduction in CO₂ emissions of around 60%. The remaining 40% must be eliminated by carbon capture, utilization, and storage (CCUS).
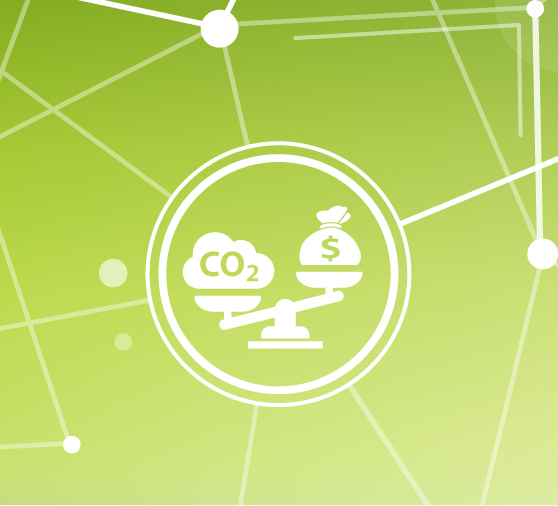
LIQUID AMINE PROCESS
ANDRITZ has deployed a liquid amine process for the pilot plant. This technology is currently the most mature and commercially viable approach for largescale applications. It uses amines — organic compounds derived from ammonia (NH3) – to “scrub” the CO₂ from the flue gas. At lower temperatures the amines bind to CO₂ and absorb it. When heated, they desorb it to yield close to pure carbon dioxide.
There are two advantages to the amine process. First, it offers a high removal rate – up to 95% is a good practical value. Second, it produces a high purity CO₂ product – up to 99.9% without purification. Once separated, the CO₂ is cooled, further purified, and compressed. It can then be permanently stored underground or processed for use.
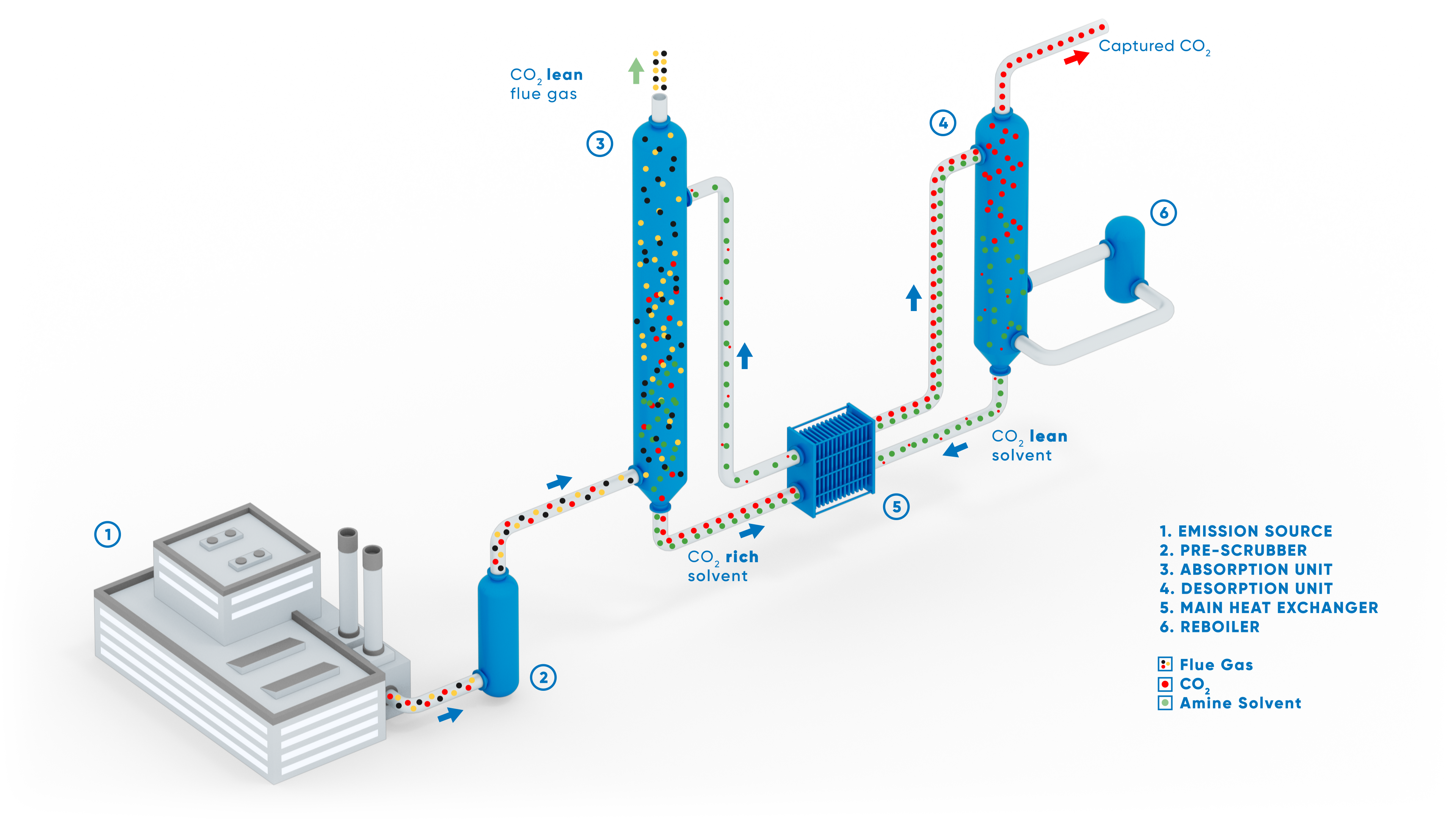
OPPORTUNITIES FOR THE PULP AND PAPER INDUSTRY
This process opens interesting opportunities for the pulp and paper industry, since its CO₂ is considered to be of biogenic origin. Due to its high level of purity, the captured CO₂ can be used within the pulp mill itself, for example, to precipitate and recover lignin from black liquor, which can then be used to produce polymers or biofibers. Other opportunities for the use of the captured CO₂ include the production of e-fuels, like e-methanol or e-methane, or green ammonia.
Since the product portfolio from ANDRITZ also includes systems for green hydrogen and e-fuel synthesis, comprehensive support can be provided to pulp mills wishing to explore these opportunities.
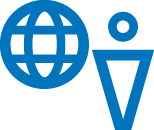
Would you be interested to discuss your CO₂ Capture, Utilization and Storage plan with one of our experts?