Would you be interested to discuss your CO₂ Capture, Utilization and Storage plan with one of our experts?
Chemical absorption / desorption process
The chemical absorption process has been used since the 1930s to capture CO₂ from ammonia plants for food applications. Today it remains the most mature process for large scale CO₂ capture.
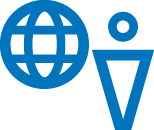
Several solvents are available for CO₂ capture by chemical absorption. The most commonly used solvent is based on the primary amine monoethanolamine (MEA) and/or mixtures of secondary/tertiary amines, usually with the addition of promoters such as piperazine.
Based on its previous experience with CO₂ capture plants and its expertise with gas-liquid absorbers, ANDRITZ selects the most suitable solvent blend for a given CO₂ concentration in the flue gas and a targeted capture rate. Depending on the customer's solvent preference, ANDRITZ can also design a solution based on hot potassium carbonate (HPC).
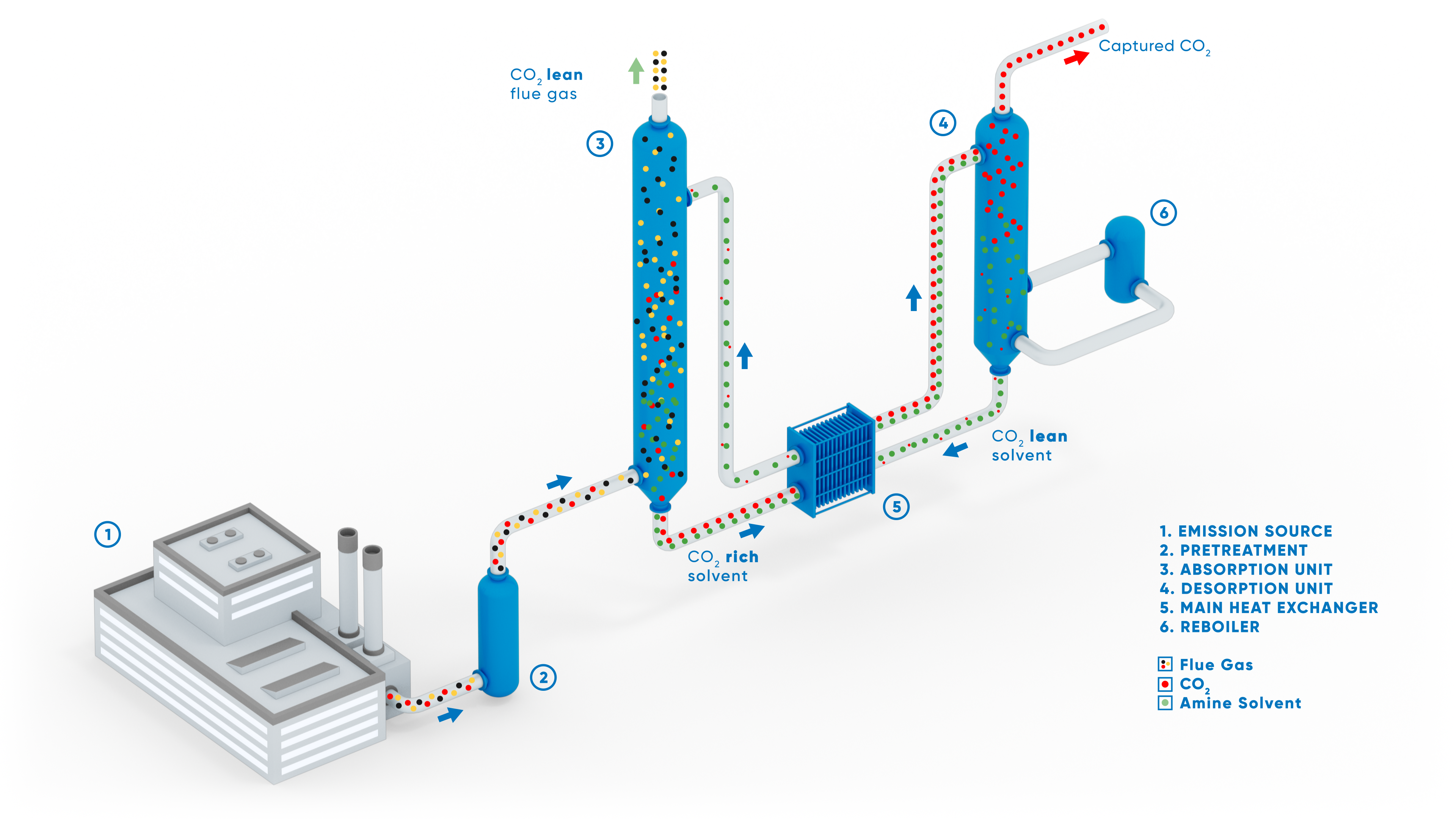
ANDRITZ Carbon Capture - Chemical Absorption (Amines)
As shown in the figure, for an amine-based solvent, the CO₂-rich flue gas from the industrial process first enters a pre-scrubber where it is cooled (or quenched) and further treated to remove certain contaminants (acid gases, particulates, etc.) that would degrade the solvent.
The flue gas then enters the absorption unit (or column) where the CO₂ is continuously absorbed (or scrubbed) by the solvent. The absorption process utilizes the reversible chemical reaction of CO₂ with the solvent. The CO₂-lean and clean flue gas leaves the top of the absorber towards the stack. The CO₂-rich solvent is transferred to the desorption unit (or stripper). Hot and partially fresh solvent from the reboiler enters the desorption unit, causing the CO₂ to be stripped from the solvent. As a result, a stream of pure CO₂ is collected at the top of the stripper. The CO₂ lean solvent is then regenerated and circulated to the absorber. The pure CO₂ stream is further processed to the required purity before being compressed, transported, or stored for future use (enhanced oil recovery, chemical synthesis, geological storage, etc.).
In the case of the HPC solvent, the figure would look slightly different as the potassium carbonate operates on a pressure swing absorption/desorption cycle as compared to the amine-based solvent which operates on a temperature swing absorption/desorption cycle.
The energy requirements for solvent regeneration (heat of desorption, sensible heat, and heat of vaporization) and the correct energy integration of the CO₂ capture unit into the industrial process are key features of the ANDRITZ CO₂ capture offering. Depending on the CO₂ concentration in the flue gas, the required amount of CO₂ to be captured, and other site-specific conditions (steam availability, steam pressure, on-site CO₂ storage, ...), ANDRITZ will design a unique solution to ensure the lowest operating costs for the removal of CO₂ from the flue gas.
The main features of the ANDRITZ amine-based chemical absorption/desorption process are:
- Low temperature absorption (30 - 50 °C)
- High temperature desorption (110 - 130 °C)
- Closed-loop operation
- Advanced amines to reduce energy consumption
- Pre-Treatment for quenching, removal of acidic pollutants and particles
- 3 - 4 bar steam required for desorption
- Recovery required to avoid high amine losses
- Heat recovery for district heating; heat pumps for steam generation
- CO₂ compression and/or liquefaction as required by the customer
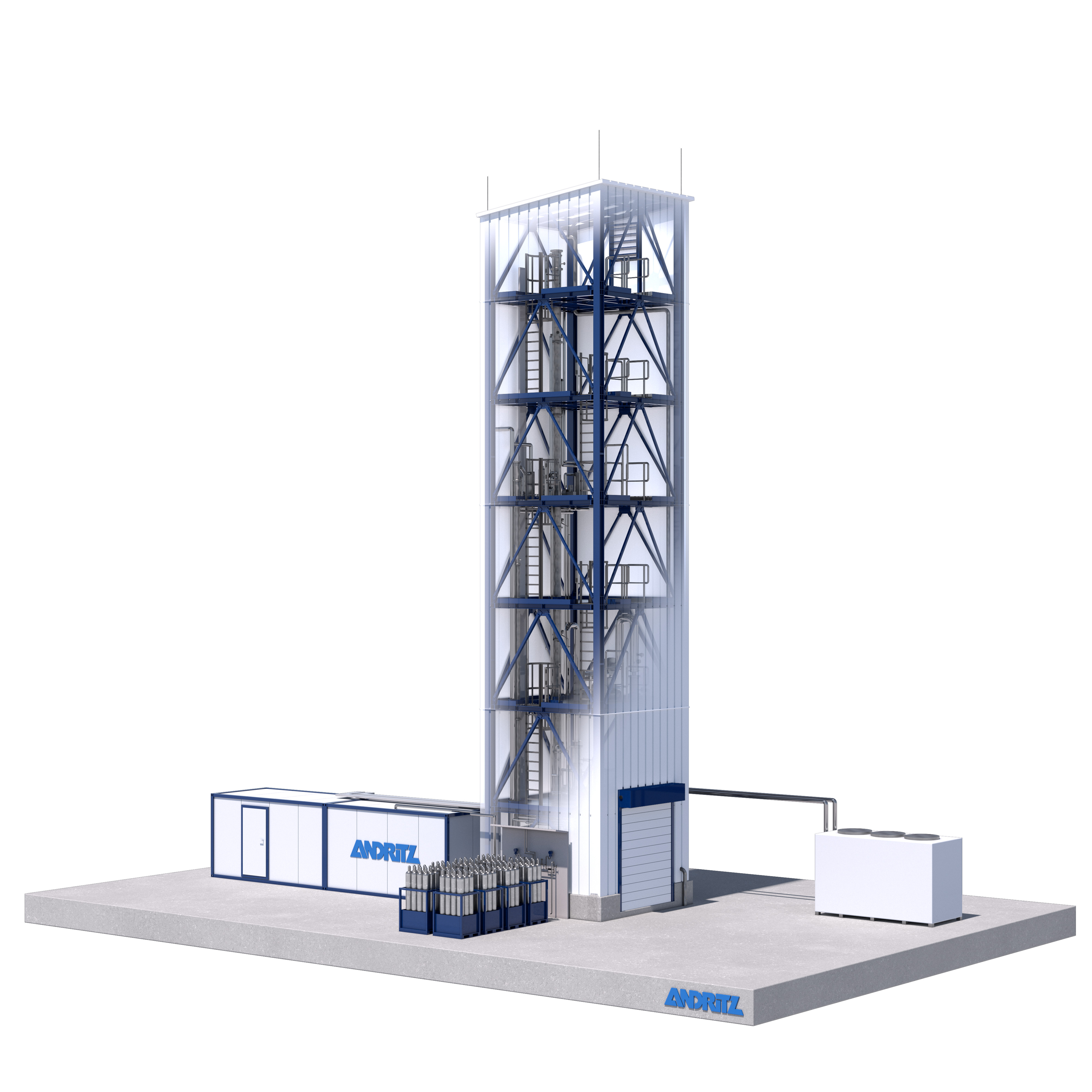
CO2 Rohrdorfer plant (Germany)