The latest advancement in LC refiners: TwinFlo Prime makes its debut
ANDRITZ engineers are continually seeking ways to make products better – through design, manufacturing methods, and/or materials of construction. The introduction of the TwinFlo Prime refiner illustrates this point.
The new TwinFlo Prime LC refiner
The ANDRITZ TwinFlo refiner is well established and proven, with over 2,000 LC refiners operating around the world, and it is a known benchmark when it comes to refiner technology.
The TwinFlo is a single-disc refiner with refining zones on both sides of the disc. The accepted state-of-the-art for adjusting the refining plate gap is to allow the rotor disc to “float” on the spline shaft, centering itself axially between the stator discs. A series of machined keyways around the circumference of the shaft serves to guide the disc as it floats on the shaft.
This works well for most applications, but there are occasions where chemical deposits in the process water tend to scale up in the keyway guides and prevent the rotor disc from floating freely. When this happens, the energy input becomes imbalanced and the refiner plates suffer uneven wear. The corrective action is to replace the plates and manually scrape the deposits out of the keyway guides – a cumbersome, expensive, and time-consuming activity.
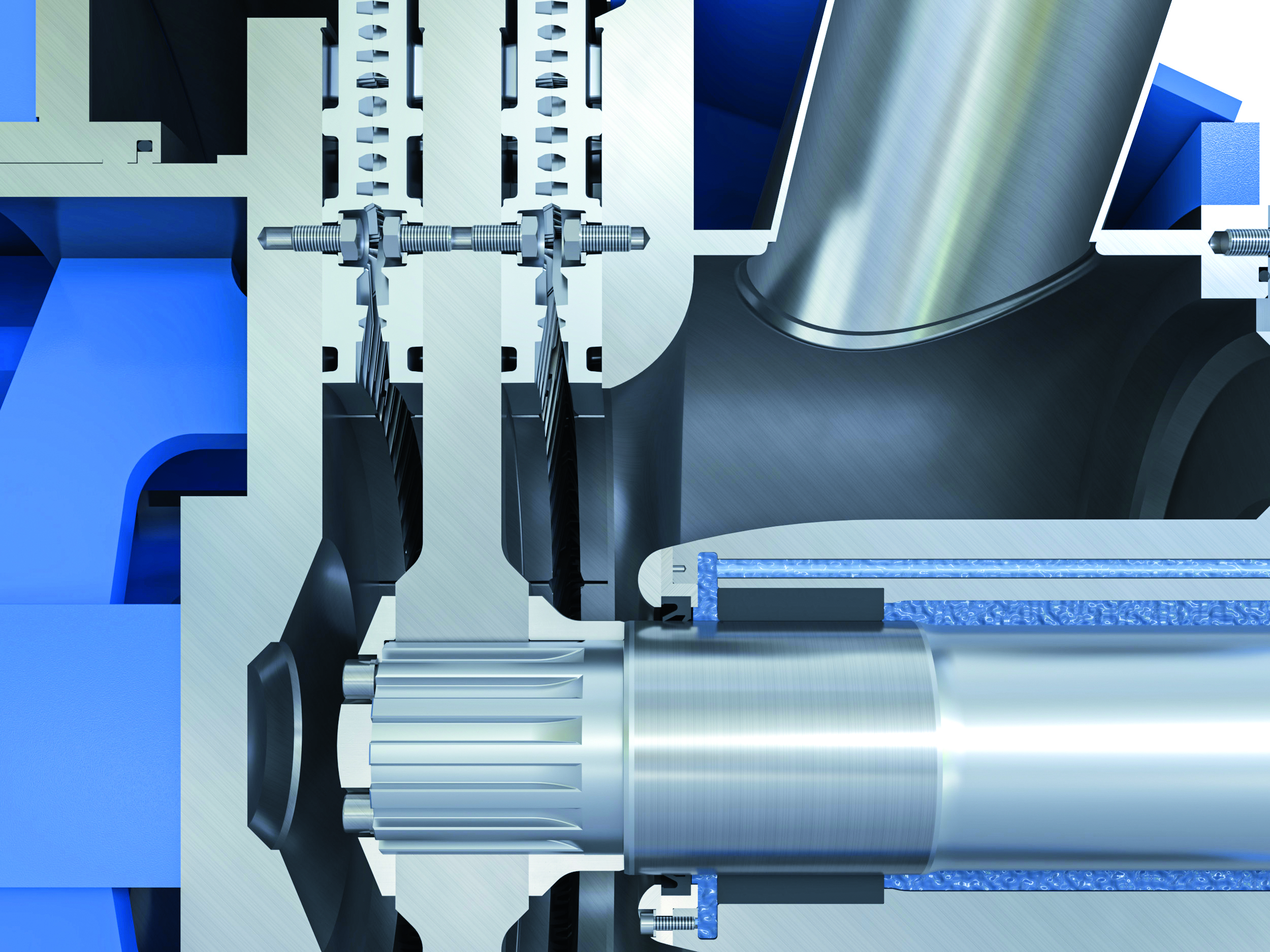
Direct connection between rotor disc and shaft
MAKING THE CONNECTION
For the new TwinFlo Prime refiner, designers at ANDRITZ have arrived at a better way to adjust the refining gap and eliminate the problems associated with deposit build-up in the keyways. The solution is to connect the rotor disc directly to the shaft so that the entire shaft and disc float as a single unit. This is the primary advancement in the TwinFlo Prime LC refiner.
The bearing unit is special. Instead of roller bearings, a hydrodynamic plain bearing is installed, which uses sealing water as the lubricating fluid instead of oil. Only with this new bearing design is it possible to secure the rotor disc on the shaft as this type of bearing allows considerable movement in axial direction.
A RANGE OF BENEFITS
Not only does the fixed connection between rotor disc and shaft in the new refiner improve its ability to maintain an optimum plate gap, it contributes several other key benefits, too:
Compact size. The length of the TwinFlo Prime is approximately 30% shorter than conventional TwinFlo models. Since no lubricating oil is used for the bearing, there is no risk of oil contaminating the stock in the event of a leak. Hence, there is no longer any need for a separate mechanical seal. The bearing can be situated closer to the rotating disc, shortening the overall shaft length considerably. Papermakers will appreciate the simplified equipment layout, easier transport and installation, and more space for maintenance that the smaller footprint of the TwinFlo Prime provides.
Increased energy efficiency. With the bearing unit closer to the rotating disc, shaft strength and machine stiffness are improved significantly. This enables the TwinFlo Prime to handle about 25% more power, improving specific refining performance significantly. Thus, it’s possible to install smaller refiners in the same application.
Optimized pulp flows. Simplifying the connection between rotor disc and shaft creates an opportunity to enlarge the disc port openings by about 70%, improving the pulp flow and equalizing the distribution of stock suspension as it splits between the two refining zones.
Dampening mechanism. Starting up a refiner creates significant force as stock rushes in and pushes forcefully against the rotor disc. This pushing force can sometimes be sufficient to close the refining gap on one side of the disc so that the rotor disc is no longer able to float back and center itself. The result is poor refining performance and unnecessary plate wear. The TwinFlo Prime has a viscous dampening mechanism inside the bearing that absorbs these initial forces and prevents fast movement of the shaft during the initial high flow at start-up.
Simplified operation and maintenance. Eliminating oil contamination from a bearing that may leak is a major positive for operation and maintenance. In addition, the design of the new refiner significantly reduces the time required to dismantle the unit for a bearing change or to access key components. The bearing unit has a cartridge design for ease of changing out.
Simple mechanical seals are now used, and the seal also has a cartridge design for easy replacement. The work can be done without having to lift the refiner or drive unit off its foundation.
The even distribution of stock and uniform application of power eliminate one-sidedness in refiner plate wear. This extends plate life and reduces downtime for changes.
TwinFlo (left) vs. TwinFlo Prime (right) size comparison
SUMMARY
The fixed connection between rotor disc and shaft in the TwinFlo Prime improves the way the refining gap is adjusted and eliminates potential problems due to deposits building up in the floating mechanism. In addition, it offers several key benefits: a much more compact size, increased energy efficiency, higher possible installed motor power, optimized pulp flows in the refiner, increased plate life, and easier maintenance.