ANDRITZ Lignin Recovery technology for kraft mills
The benefits to installing Lignin Recovery technology in a kraft mill include the ability to debottleneck a recovery boiler and the potential cost savings from substituting a sustainable biofuel for purchased fossil fuels. Lignin is also being utilized as a sustainable, renewable raw material for advanced bioproducts such as composites or as a substitute for phenolic and aromatic compounds, which might create an additional revenue stream for a kraft mill.
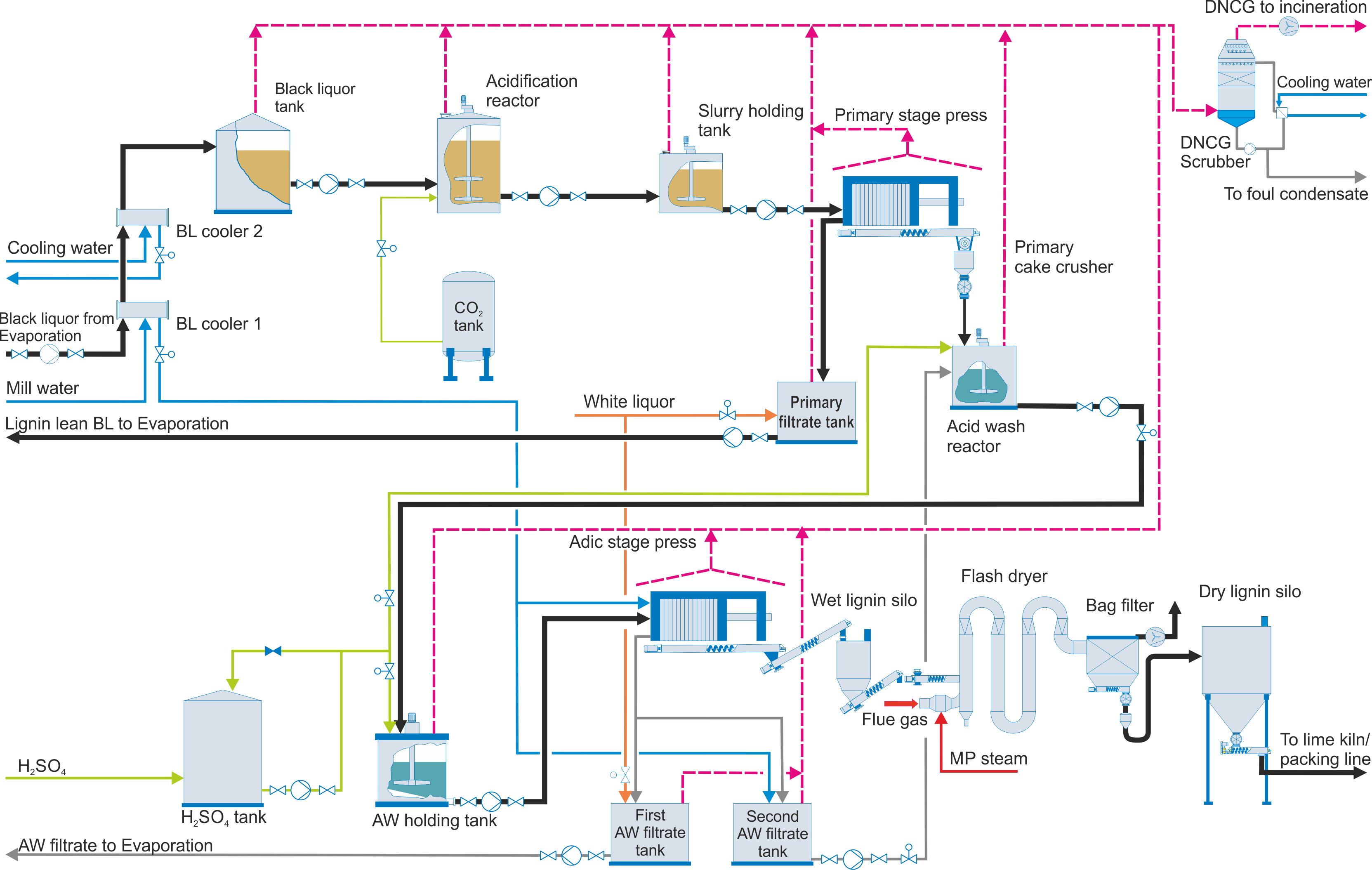
The ANDRITZ LignaRec lignin recovery process