Automation: Looking out beyond the edge
In the near future, Edge computing has the potential to accelerate the evolution – perhaps even prompt an evolution – in industrial automation beyond what we have witnessed in recent years. Here are some of the benefits of using Edge devices.
More computing power in smaller packages. Greater connectivity. And, at last, an accepted communications protocol. These are the drivers that are pushing industrial automation away from centralized nodes out to the very extremes (edges) of a plant’s network. By gathering data, crunching it, and running the control routines at the source – small, powerful Edge devices can control virtually anything. And, they are easily connected through the Internet to coordinate with each other.
Imagine an assembly line with 10 five-meter conveyor belts, each equipped with an Edge device. The flexibility to start, stop, run forward or backward, and control the speed of each belt is there – PLUS the ability to operate them as if they were one 50-meter belt. Or, more pertinent to our industry, imaging the sections of a paper machine each equipped with an Edge device. Precise control of the headbox, forming, pressing, coating, drying, and finishing sub-processes PLUS optimized machine control.
Local control and plantwide connectivity is that simple with Edge devices.
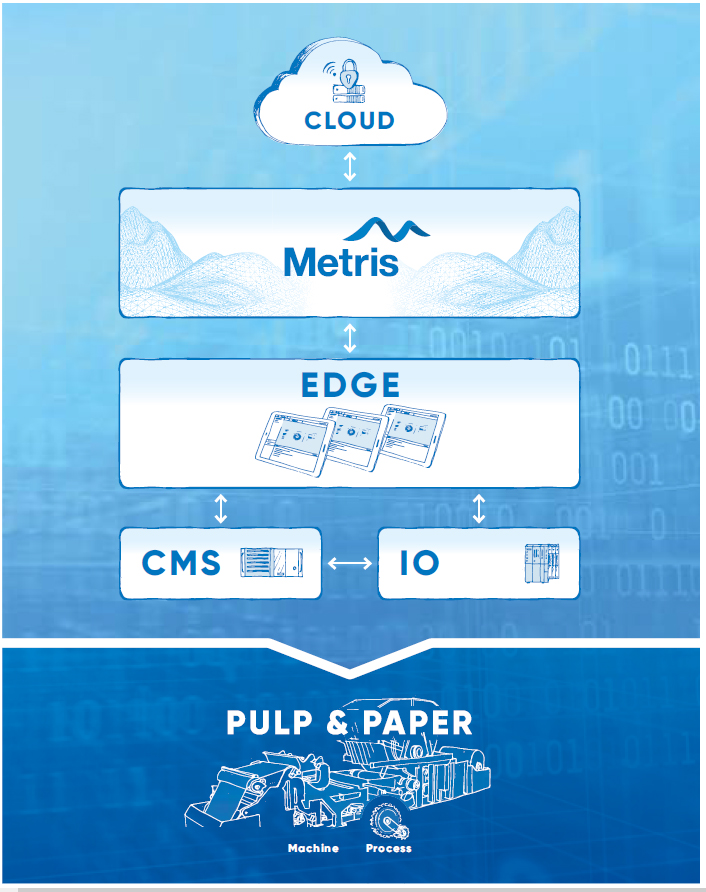
How does that compare to what we are doing now? Today, a classic industrial automation network relies on a rather rigid hierarchy in order to operate. There are field devices (instruments and valves) providing the basic input/output … connected to programmable controllers that execute the control tasks ... connected to a server (or servers) that provide the main control … which are equipped with operator stations for visibility. Optimization software is separate. The topology of this classic network can be complex, is usually tailor-made, and is programming-intensive. More importantly, current networks that use a patchwork of incompatible protocols appear to lack the performance and capacity needed to meet growing demands.
An Edge device, on the other hand, combines the input/output, condition monitoring, and complete control in a small package. It performs complete control at the unit level (equipment or major sub-system) and can be easily linked with other Edge devices to perform machine automation or complete process automation. It is “configured” rather than “programmed” using a highly graphical, functional interface. Of special interest is that these Edge devices have immediate or direct connection to the Internet or an external non-propriety network. The device itself provides translation between networks that use different protocols using the industry-standard protocol (OPC UA TSN), which has emerged as an excellent solution of real-time, vendor-neutral network communications.
Of importance to us at ANDRITZ is that Edge devices are highly compatible with our Metris X and Metris OPP systems, which are already platform-independent automation and optimization solutions. We can think of Edge devices as being the individual members of an orchestra (each playing the notes on their music sheets) with Metris acting as the conductor. There is clear potential for Edge computing in the pulp, paper, and power industries and we will keep looking out beyond the edge.